Die Feder – Ein Dachbegriff für zahlreiche Produkte
Sie findet sich in Computertastaturen, in Schließzylindern, in ganz unterschiedlichen Ausführungen in jedem Auto, in zahllosen Maschinen und unzähligen weiteren Anwendungen. Zweifellos – ohne die technische Feder und ihre Elastizität würde die Welt, wie wir sie heute kennen, nicht funktionieren. Kaum ein anderes Bauteil existiert in einer solchen Vielfalt und in entsprechend zahlreichen Bauweisen.
Die Feder
Genereller technischer Überblick
Aus technischer Sicht handelt es sich bei einer Feder um einen nach vorgegebener Geometrie gestalteten Körper, der durch seine Formgebung und die Materialeigenschaften eine besondere elastische Verformbarkeit besitzt – über einen großen Zeitraum hinweg und ohne Ermüdungserscheinungen. Dadurch ist die Feder in der Lage, potenzielle Energie zu speichern. Die Einteilung erfolgt dabei nach der Art der auftretenden Beanspruchung:
- Druck und Zug
- Biegung
- Torsion (Verdrehung)
Der Großteil der heute genutzten Metallfedern arbeitet über Biegung und Torsion. Druck- und zugbeanspruchte Federn werden in deutlich kleineren Anwendungsnischen benötigt. Dennoch verbleiben genügend unterschiedliche Federarten – diese enorme Vielfalt ist auch ein Grund, warum es so wenige Druck- und Zugfedern gibt. Das Anwendungsspektrum kann weitgehend von Biege- und Torsionsfedern bedient werden. Aus der Unterteilung der drei grundlegenden Arten ergibt sich folgende Unterteilung:
Druck- und Zugfedern | Biegefedern | Torsionsfedern |
---|---|---|
|
|
|
|
|
|
Die jeweiligen Federarten lassen sich schließlich noch weiter in unterschiedliche Bauweisen aufteilen. Was die Materialwahl bei metallischen Federn anbelangt, so kommen hier praktisch ausschließlich Stahl sowie, in deutlich geringerem Maß, legiertes Kupfer zum Einsatz.
Die verwendeten Stähle werden unter dem Dachbegriff Federstahl zusammengefasst – Stahl mit einer durch Legierungsstoffe besonders hohen Festigkeit bei gleichsam hoher Elastizität. Dadurch können Federstähle einerseits bei der Bauteilproduktion plastisch verformt werden, andererseits jedoch bei der Anwendung unzählige elastische Verformungen mitmachen, ohne dass es zu Ermüdungserscheinungen kommt.
Bemessung der Federcharakteristik
Die beiden wichtigsten Maßeinheiten zur Bestimmung der Federcharakteristik (und damit auch für die Auswahl eines bestimmten Federtyps aus einem bestimmten Stahl) sind:
- Die Federkonstante, nach DIN auch als Federrate oder Federsteifigkeit bezeichnet. Dabei handelt es sich um den Quotienten aus Dehnung und Kraft. Mit dieser Konstante kann bei bekannten Kräften vornehmlich die Federgröße ermittelt werden.
- Die Federkennlinie: Sie erlaubt Rückschlüsse auf die Charakteristik einer Feder beim Einwirken von Kraft. Genauer: das Verhältnis von Federkraft über den möglichen Federweg. Dabei unterscheiden sich drei Arten:1. degressive Kennlinien, bei denen mit zunehmendem Federweg die Kraft verringert wird
2. lineare Kennlinien, bei denen die Kraft über den Federweg gleichbleibt
3. progressive Kennlinien, bei denen die Kraft mit zunehmendem Federweg ansteigt
Zusammen mit den bekannten Materialeigenschaften stehen auf diese Weise alle Grundlagen zur Verfügung, um den richtigen Federtyp auszuwählen.
Wichtige Druck- und Zugfedern im Überblick
Die Stabfeder
Bei der Stabfeder als Druck- und Zugfeder handelt es sich um eine der technisch simpelst-möglichen Ausprägungen der Feder. Sie wird heutzutage allerdings nur in wenigen Fällen aus metallischen Werkstoffen hergestellt. Deutlich häufiger ist die Verwendung von Kunststoffen. Der wichtigste moderne Einsatzzweck dieser Feder ist der eines Puffers, vornehmlich zur Lagerung schwererer Bauteile oder Aggregate auf elastische Art und Weise.
Eine typische Anwendung wäre beispielsweise die Lagerung einer industriellen Fertigungsanlage auf Elastomerblöcken, welche Vibrationen „schlucken“ und somit die Anlage ruhiger laufen lassen.
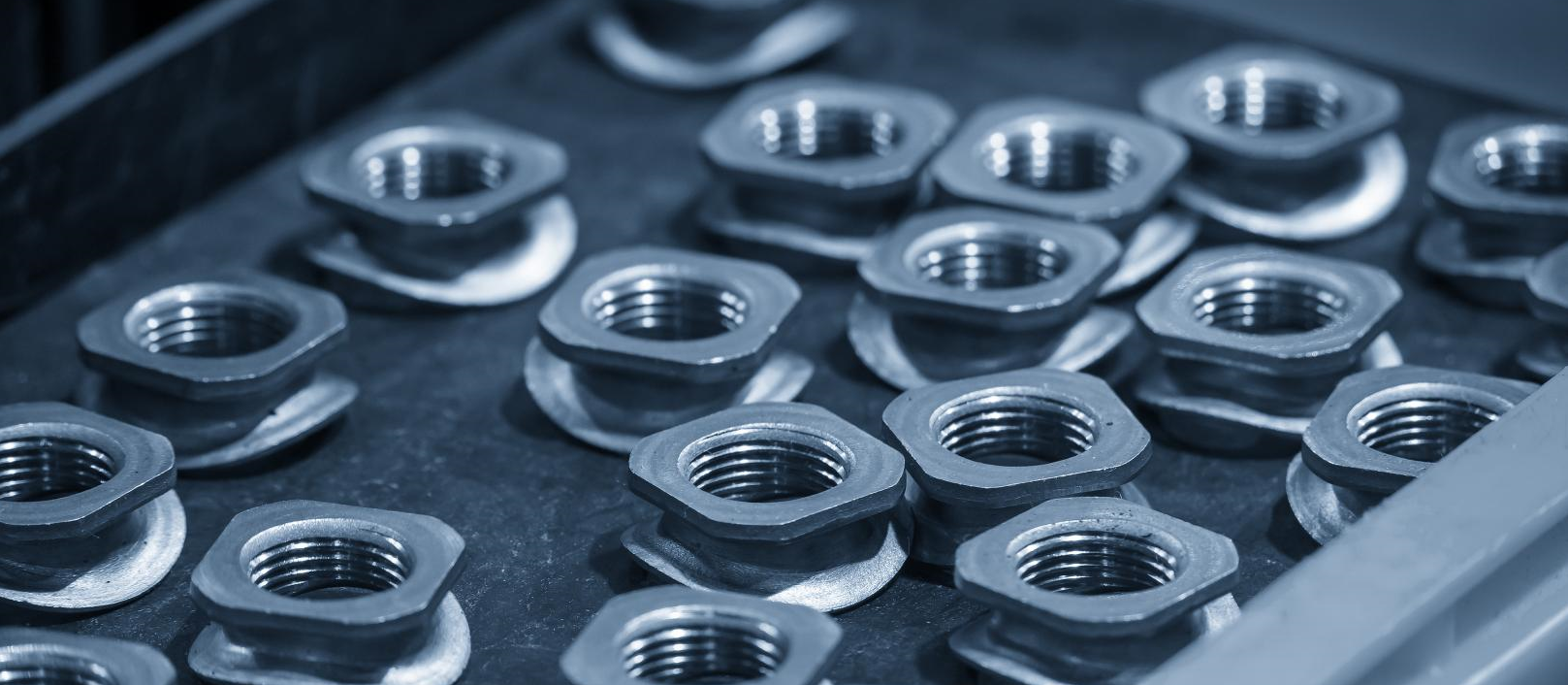
Die Tellerfeder
Tellerfedern zeigen sich typischerweise als Kreisringscheibe – ähnlich beispielsweise zu einer Unterlegscheibe. Im Gegensatz zu dieser sind Tellerfedern jedoch zu einer leichten Kegel- oder Halbbogenform gebogen. Meist erfolgt das Einfedern hierbei auf Druck, wobei sich der Durchmesser der Kreisringscheibe vergrößert. Im englischsprachigen Raum wird diese Feder als Belleville Washer bezeichnet, nach dem französischen Erfinder Julien Belleville.
Eine Nutzung kann sowohl in Form einzelner Tellerfedern wie aus zusammengesetzten Federsäulen (Kombination mehrerer Tellerfedern) erfolgen. In diesem Fall werden die Federn mindestens paarweise um je 180 Grad gedreht installiert, je nach Zielsetzung gibt es auch andere Kombinationen. Werden diese Federsäulen außen nicht durch einen Hohlzylinder gesichert, kann eine Stabilisierung alternativ über einen durch das mittige Loch geschobenen Stab erfolgen.
Da Tellerfedern eine sehr hohe Federkonstante auf kleinem Raum aufweisen, werden sie meist in Anwendungen genutzt, bei denen sehr große Kräfte auftreten. So werden beispielsweise Flugzeugpropeller auf ihrer Nabe mithilfe von Bolzen gesichert, die mit Tellerfedern unterlegt sind. Auch als Ventilfedern finden sich viele Anwendungsbeispiele.
Wichtige Biegefedern im Überblick
Die Blattfeder
Die Blattfeder gehört zu den ältesten und in einigen Ausprägungen technisch einfachsten Federn, denn sie besteht aus unterschiedlich gebogenen Bandstahlelementen. Die wichtigsten Vertreter dieser Federart sind die Folgenden:
- Die Elliptikfeder: In der simpelsten Ausführung, der Halbelliptikfeder, handelt es sich dabei um nicht mehr als ein oder mehrere im Grundzustand gleichmäßig durchgebogene Bandstahlelemente – meist mit mindestens einem zum Auge rundgebogenen Ende zur Befestigung.Werden mindestens zwei davon mit der konkaven Seite zueinander weisend verbunden, wird daraus eine Vollelliptikfeder. Die Elliptikfeder war lange Zeit die wichtigste Feder im Fahrzeugbereich. Sie spielt heute jedoch nur noch im Transportsektor eine Rolle.
- Die Parabelfeder: Dies ist eine parabel- oder, seltener, trapezförmige Blattfeder, die sich zu den Enden verjüngt. Wegen der daraus resultierenden anderen Federcharakteristik im Vergleich zur (Halb-)Elliptikfeder wird sie häufig als Alternative zu dieser im Fahrzeugbereich genutzt. Eine weiterhin große Bedeutung hat die Parabelfeder im Eisenbahnsektor zur Federung der Radsätze an Waggons und Lokomotiven.
- Die Spiralfeder: Hier ist eine Blattfeder zu einer mehrlagigen Schnecke aufgewickelt. Sie wurde einst in vielen Anwendungen als Federantrieb genutzt (etwa in Grammophonen). Heute spielt sie jedoch praktisch nur noch in mechanischen (Armband-)Uhren eine maßgebliche Rolle.
- Die Wellenfeder: Eine Kreisringscheibe, teils als Spirale oder Säule ausgeführt, die über ihre ganze Länge wellenförmig gebogen ist. Bei vergleichbarer Federkonstante ist sie dadurch eine kompaktere (niedrigere) Alternative zur Schraubenfeder. Wegen der aufwendigeren Herstellung wird sie heute vor allem in industriellen Spezialanwendungen genutzt. Etwa als Axialdichtung für Wellen sowie in Ventilen.
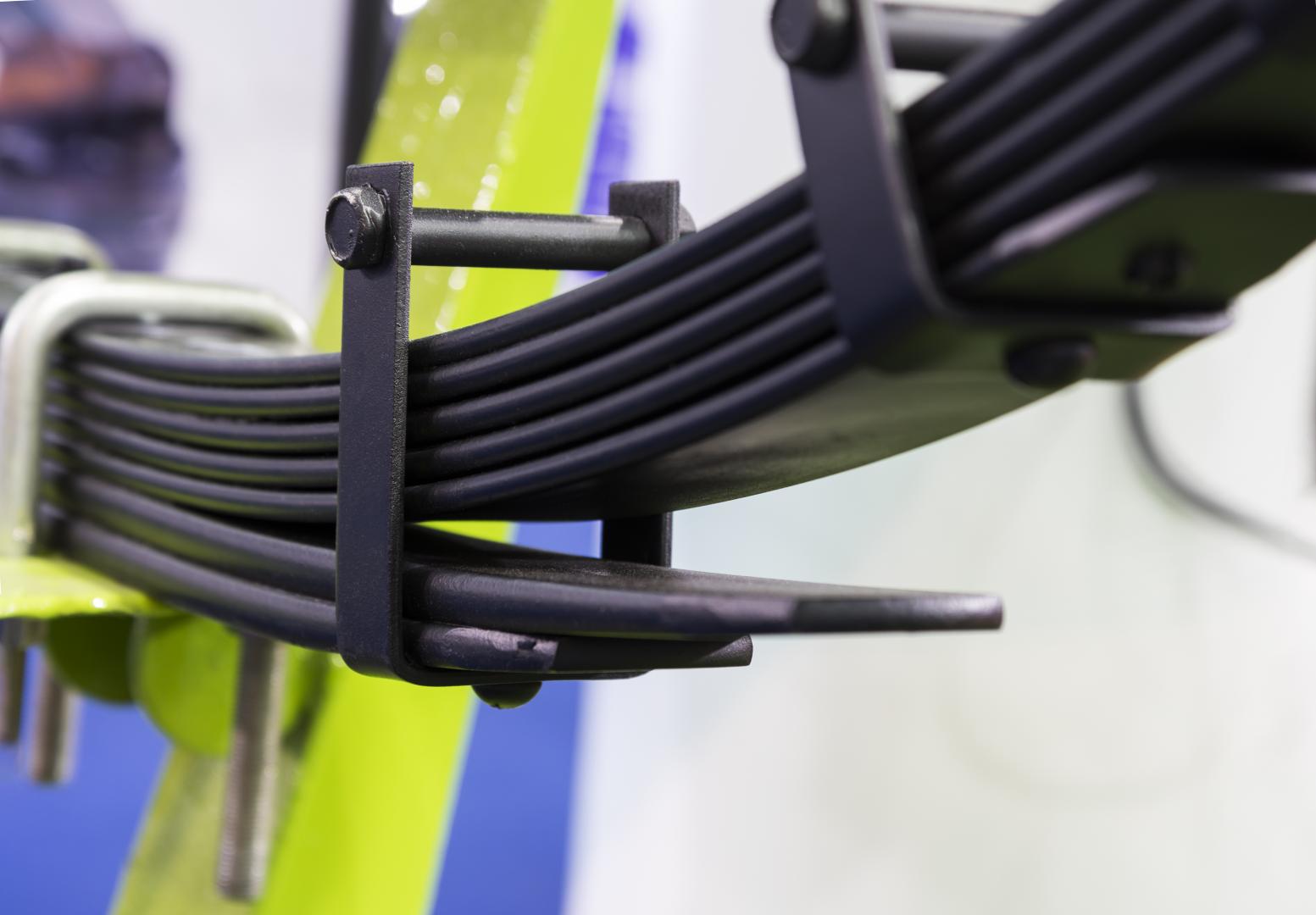
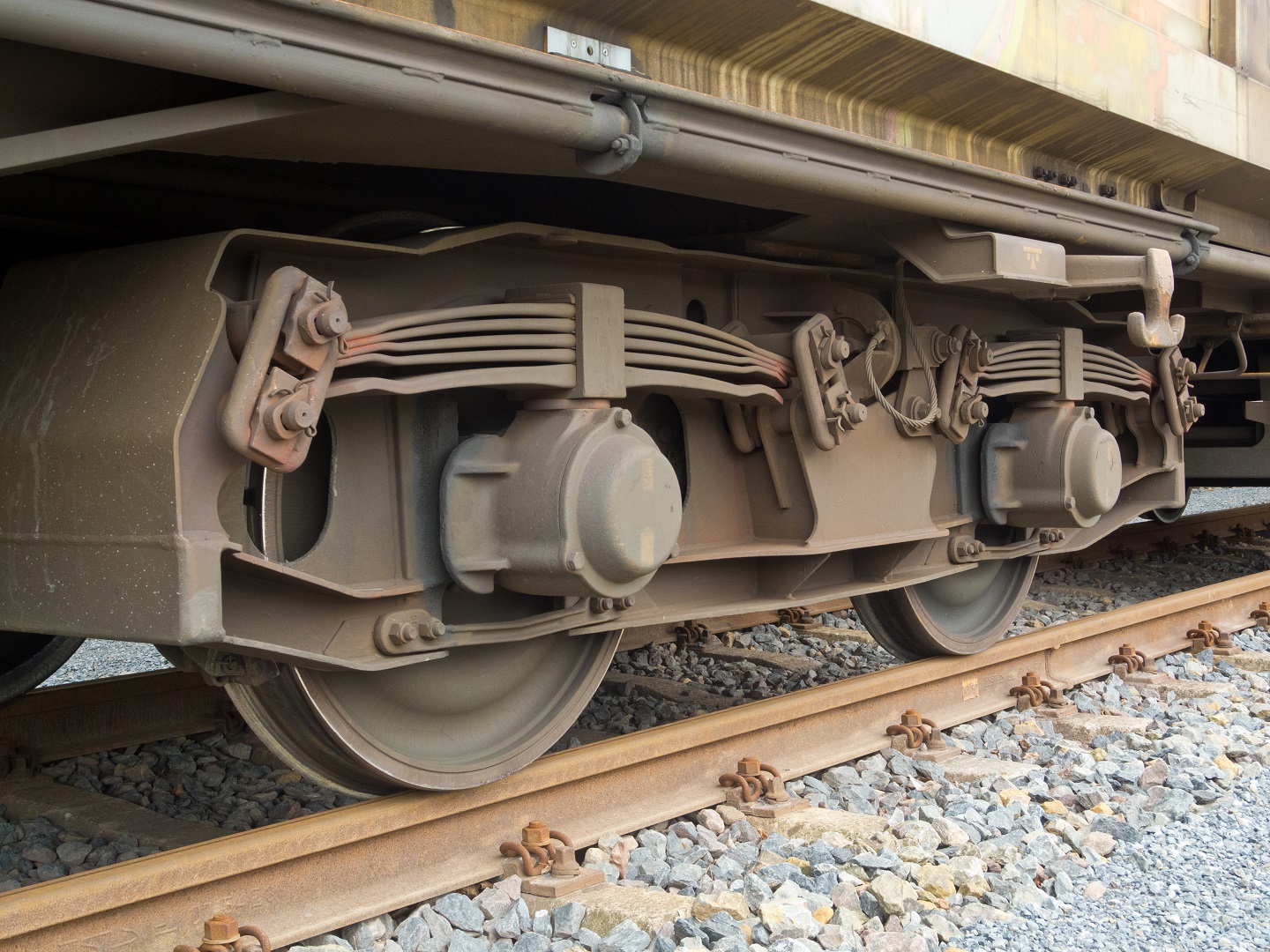
Die Drahtfeder
Der maßgebliche Unterschied der Draht- zur Blattfeder liegt in der Tatsache, dass bei ersterer als Ausgangsmaterial kein Band-, sondern (dünnes) Rundstabmaterial bzw. Draht eingesetzt wird. Teilweise werden auch die bereits erwähnten Wellenfedern auf diese Weise hergestellt. Die beiden wichtigeren Anwendungen sind jedoch:
- Die Nadelfeder: Dabei handelt es sich um einen in einfachen Formen oder auch gar nicht gebogenen Rundstababschnitt. Sie wird heute meistens dort angewendet, wo nur sehr geringer Bauraum vorhanden ist und keine großen Federkräfte benötigt werden. Wichtig ist die Nadelfeder im Instrumentenbau, auch bei Lackiergeräten und Nähmaschinen wird sie häufig verwendet.
- Die Schenkelfeder: Hierbei wird der Draht zu mindestens einer engen Schraube gewickelt, es verbleiben jedoch lange gerade Enden, welche als Hebelarme zur Einleitung der Kraft dienen. Die wohl archetypischsten Anwendungen der Schenkelfeder finden sich in der Sicherheitsnadel sowie bei der Wäscheklammer. Darüber hinaus werden Schenkelfedern in zahlreichen industriellen Anwendungen genutzt.
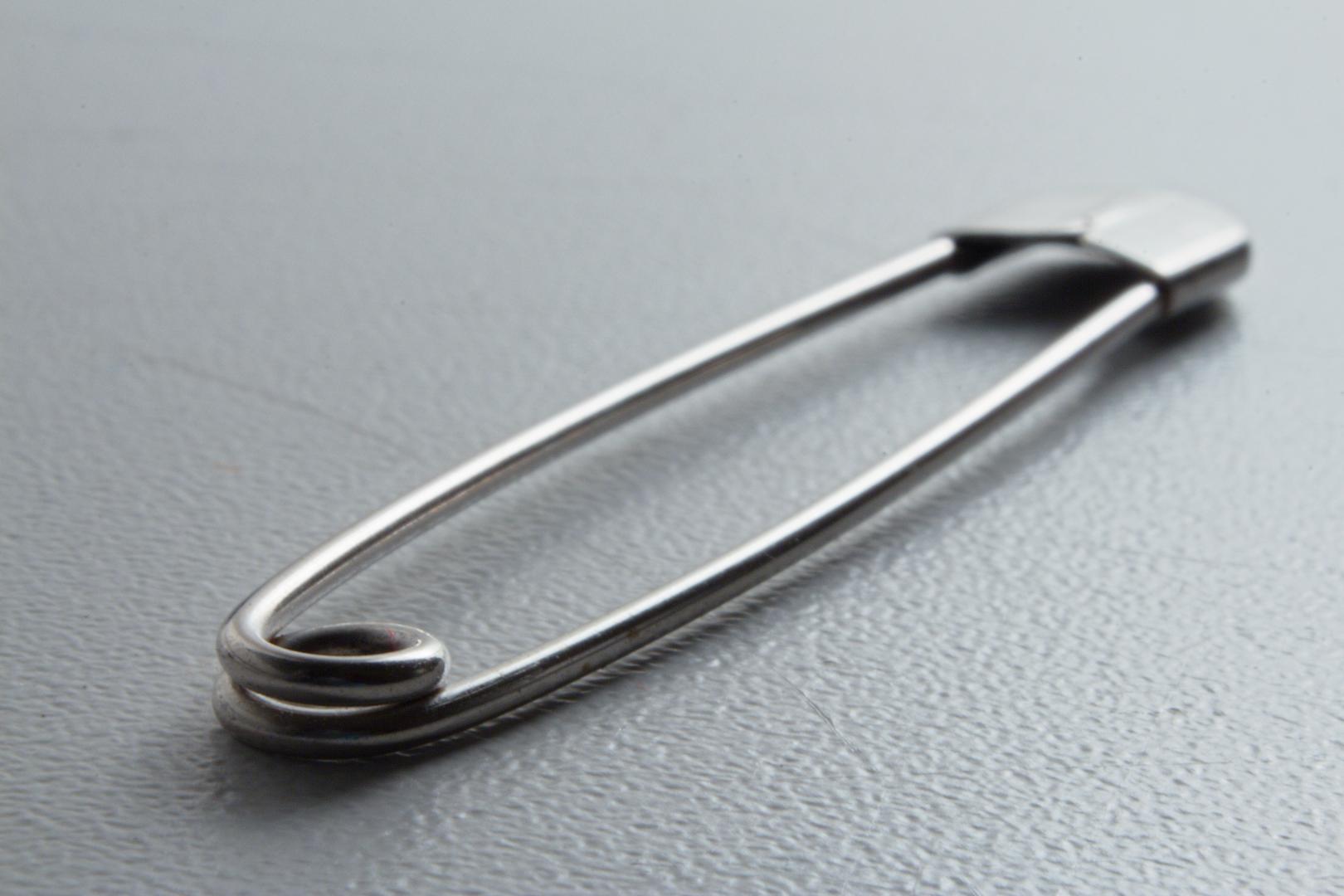
Wichtige Torsionsfedern im Überblick
Die Drehstabfeder
Praktisch alle Torsionsfedern besitzen eine Gemeinsamkeit: Sie basieren auf Rundstäben unterschiedlichster Durchmesser als Ausgangsmaterial. Andere Querschnitte existieren zwar, sie kommen jedoch ausschließlich bei einigen wenigen Spezialanwendungen zum Einsatz.
Bei der Drehstabfeder handelt es sich ebenfalls um einen solchen Rundstab – und zwar in der Form der tatsächlich einfachsten Feder. Sie weist keine Biegung auf und wird nur an einem Ende befestigt. Dazu ist sie zumindest in der Nähe des anderen Endes drehbar gelagert und entwickelt ihre Federwirkung dadurch, dass sich am anderen Ende ein Hebelarm befindet, welcher den Stab auf diese Weise in sich verdrehen kann.
Der heute grundsätzlich wichtigste Einsatzbereich der Drehstabfeder ist der automobile Sektor. Vor allem bei manchen PKW wurde und wird diese Variante als Fahrwerksfeder eingesetzt.
Die bedeutendste Anwendung des Drehstabs liegt allerdings im militärischen Bereich, konkret bei Panzerfahrzeugen. Die Gründe dafür:
- Der Drehstab kann ohne großen Aufwand in die Fahrzeugwanne integriert werden, wo er vor äußeren Einflüssen geschützt ist.
- Im Vergleich zur Federkraft haben Drehstäbe sehr geringe Durchmesser und deshalb kompakte Bauhöhen. Gegenüber anderen Federarten reduzieren sie den ohnehin geringen, beengten Innenraum in derartigen Fahrzeugen kaum.
Tatsächlich hat sich die Drehstabfederung deshalb in diesem Sektor schon seit Jahrzehnten zum Maßstab entwickelt, von dem es kaum nennenswerte Ausnahmen gibt.
Ein weiterer, nicht nur für das Militär sehr wichtiger, Vorteil von Drehstäben besteht darin, dass diese sehr leicht vorgespannt werden können, wodurch sich die Fahrzeughöhe, die Bodenfreiheit oder verschiedene Belastungszustände auf einfachste Weise anpassen lassen.
Die Schraubenfeder
Die Schraubenfeder besteht praktisch immer aus schraubenförmig gewundenem Rundmaterial. Zwar wird dieses beim Einwirken von Kräften auch auf Biegung beansprucht, dies stellt jedoch nur einen sehr geringen und je nach Enge der Biegung und Materialdurchmesser völlig vernachlässigbaren Einfluss dar.
Die primäre Arbeitsweise der Schraubfeder funktioniert über ein Torsionsmoment, welches axial zur Mittelachse der Schraube verläuft. Eine grundsätzliche Unterteilung der Schraubenfeder erfolgt nach Richtung der vorgesehenen Krafteinwirkung:
Schraubendruckfeder
Zwischen den einzelnen Wicklungen besteht ein Abstand. Durch Krafteinwirkung wird die Feder zusammengedrückt – maximal, bis sich die einzelnen Wicklungen berühren und aufeinanderliegen.
Typische Beispiele sind die Federn von Stoßdämpfern in Fahrzeugen oder im Kugelschreiber.
Die einzelnen Wicklungen können hier im Ruhezustand aufeinanderliegen oder einen Abstand aufweisen. Bei Krafteinwirkung wird die Spirale (weiter) auseinandergezogen. Die Enden sind meist als Ösen ausgeformt.
Ein typisches Beispiel sind die Federn an Garagentoren.
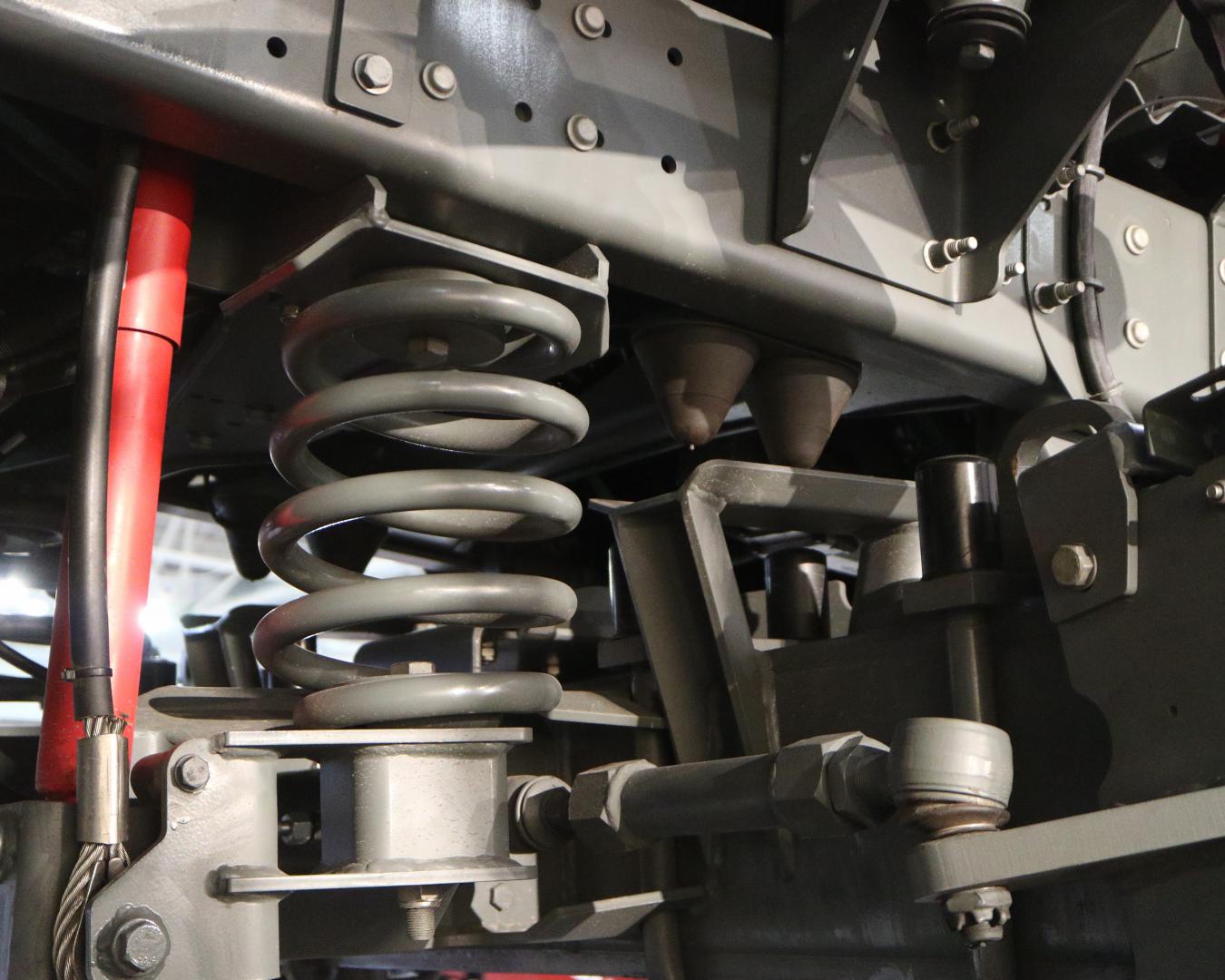
Dabei kommen bei beiden Arten der Schraubenfedern drei maßgebliche Varianten für die Formgebung zum Einsatz:
Die zylindrische Schraubenfeder: Alle Wicklungen weisen hier denselben Durchmesser auf. Gegebenenfalls verringert sich an den Enden der Steigungswinkel zu den darunterliegenden Windungen oder der Rundstab wird oben abgeflacht, um an beiden Enden eine gleichmäßige Auflagefläche über den gesamten Durchmesser zu erzielen.
Die mögliche Minimallänge ist hierbei der addierte Durchmesser aller Rundstäbe in der Wicklung. Das bedeutet, ist die Feder voll eingefedert, berühren sich die Wicklungen in axialer Richtung; eine weitere Reduktion ist nicht möglich
Die kegelförmige Schraubenfeder: Hier werden die Wicklungen mit zunehmender Höhe immer enger. Je nach Anwendungsgebiet geschieht dies auf eine Weise, durch die sichergestellt ist, dass eine voll eingefederte Feder nur wenig höher ist als der Rundstabdurchmesser einer Wicklung. Das heißt, eine voll eingefederte kegelförmige Schraubenfeder ähnelt grob einer Spiralfeder.
Die tonnenförmige Schraubenfeder: Sie besteht prinzipiell aus zwei übereinanderliegenden kegelförmigen Schraubenfedern, wobei der größte Durchmesser in der Mitte der Feder erreicht wird und die beiden Enden (typischerweise) denselben, geringsten Durchmesser besitzen. Verjüngt sich bei dieser Bauweise der Rundstabdurchmesser zu den Enden, so spricht man von einer Miniblockfeder.
Neben der möglichen Bauhöhe und dem Durchmesser werden diese unterschiedlichen Bauweisen vor allem hinsichtlich ihrer Federkennlinien ausgewählt. Weitere Möglichkeiten zur Beeinflussung der Federeigenschaften sind etwa der Einsatz von sich verjüngendem Stabmaterial oder es werden gezielt größere und kleinere Steigungswinkel genutzt.
Die Schraubenfeder bietet einen besonders großen Einsatzbereich. Ihre maßgebliche Rolle liegt heute in vielfältigen Ausprägungen im Automobilsektor und wird dort sowohl bei den Fahrwerken als auch beim Antrieb genutzt – etwa als Ventilfedern von Verbrennungsmotoren. Daneben findet sich die Schraubenfeder jedoch in kleinsten Anwendungen – als Rückstellfeder bei Computertastaturen ebenso wie in Sitzmöbeln, aber auch in Großprojekten bis hin zum Brückenbau und dem Schutz von Hochhäusern gegen Erdbeben.
Bildquellen:
Bild 1: stock.adobe.com, © Pixel_B
Bild 2: stock.adobe.com, © Andrey Armyagov
Bild 3: stock.adobe.com, © Pixel_B
Bild 4: stock.adobe.com, © warut
Bild 5: stock.adobe.com, © ingwio
Bild 6: stock.adobe.com, © marekb1
Bild 7: stock.adobe.com, © PhotoBetulo
Bild 8: stock.adobe.com, © Tomislav Forgo