Methoden für das spanlose Trennen
Sowohl das bewährte Stanzen als auch das Feinschneiden sind zentrale Verfahren bei der Be- und Verarbeitung von Metallblechen und Metallband. Wir werfen einen Blick auf die Unterschiede und die jeweiligen Vor- und Nachteile der Methoden. Darüber hinaus stellen wir noch weitere Fertigungsverfahren zum spanlosen Trennen vor.
Das Stanzen
Klassische Scherschneidtechnik im modernen Gewand
Stanzen ist, zumindest bei Materialien wie Blech, ein typischer Vertreter des Scherschneidens. Lediglich bei weichen Werkstoffen, etwa Kunststoff, wird Stanzen eher im Messerschnittverfahren durchgeführt. Aus diesem Grund ist Stanzen keine genormte Bezeichnung, da sich diese Technik nicht eindeutig in ein bestimmtes Trennverfahren eingliedern lässt.
Das zentrale Merkmal des Stanzens ist, dass hierbei das Obermesser immer als Stempel ausgeprägt ist, welcher exakt der Innenform der späteren Öffnung entspricht (zuzüglich des notwendigen Spalts). Dabei unterscheiden sich zwei Arten des Stanzens:
- Das klassische Stanzen, bei dem aus dem Material in einem Arbeitsschritt die fertige Öffnung herausgetrennt wird.
- Das Nibbeln bzw. Knabbern, bei dem mehrere Stanzschritte nacheinander durchgeführt werden, wodurch die fertige Öffnung erst nach und nach entsteht.
Als ein Beispiel von vielen sei hier ein Langloch in einem Blech genannt. Dies könnte in einem Arbeitsschritt durch einen entsprechend geformten Stempel hergestellt werden oder durch mehrere Schnitte mit einem runden Stempel, dessen Durchmesser maximal dem der Schmalseite des Langlochs entspricht.
Das Stanzen
Die einzelnen Produktionsschritte
Der Stanzvorgang selbst lässt sich dabei in mehrere Schritte unterteilen:
- Das Blech wird eingeführt, ein Niederhalter fährt herab und drückt es gegen die Schneidplatte, die als Untermesser fungiert. Gleichzeitig fährt der Stempel herab, bis es Kontakt zum Blech hat.
- Der Stempel wird mit Kraft beaufschlagt. Dadurch kommt es zu einer (noch) elastischen Verformung und einer beginnenden Plastifizierung.
- Der Stempel dringt so weit in das Blech ein, dass die Fließgrenze überschritten wird und es an der Schnittkante zu einer plastischen Verformung kommt.
- Die fortschreitende Krafteinwirkung sorgt in Verbindung mit den Haltekräften dafür, dass das Material nicht weiter ausweichen kann. Es kommt zu mikroskopischen Rissen, die sich fortführen bis schließlich das gesamte Blech durchtrennt ist.
- Der Stempel dringt weiter bis zu seinem unteren Totpunkt ein und stößt dabei den ausgeschnittenen Teil aus.
- Nun wird der Stempel wieder angehoben, der Niederhalter lässt das Werkstück los, es kann herausgenommen oder weitergeführt werden.
Werkstück oder Abfall?
Der sogenannte Stanzbutzen ist dabei der Teil, der durch den Stempel aus dem Material herausgeschnitten wird. Je nach Ziel des Prozesses ist er entweder ein Abfall- oder das gewünschte Produkt:
- Wird ein Lochgitter in ein Blech gestanzt, dann zählt der Butzen als Abfall.
- Werden hingegen Blechscheiben für Kronkorken ausgestanzt, stellt der Butzen das gewünschte Werkstück zur Weiterverarbeitung dar.
Hierbei zeigt sich ein wichtiger wirtschaftlicher Unterschied von spanlosen zu spanenden Trennverfahren: Ganz gleich, welcher Teil des Ausgangsmaterials zum Abfallprodukt wird, es hat immer eine weitgehend definierte geometrische Form. Durch geschickte Planung ist es möglich, diese Teile als Ausgangsmaterial für andere Produkte heranzuziehen.
Moderne Hochleistungsautomaten erlauben heute präzise Ergebnisse bei gleichzeitig enormer Geschwindigkeit. Bis zu 2.000 Stanzvorgänge sind pro Minute erreichbar. Optimal also für die Fertigung von Serienteilen aus Blechtafeln oder -streifen.
Darüber hinaus erlaubt das Stanzen die Kombination mit weiteren Bearbeitungsschritten für einen effizienten Ablauf. Direkt im Anschluss kann das Werkstück beispielsweise gebogen, geprägt, gebördelt oder auch genietet werden. Dazu ist nicht zwangsläufig ein Weitertransport oder Umspannen notwendig.
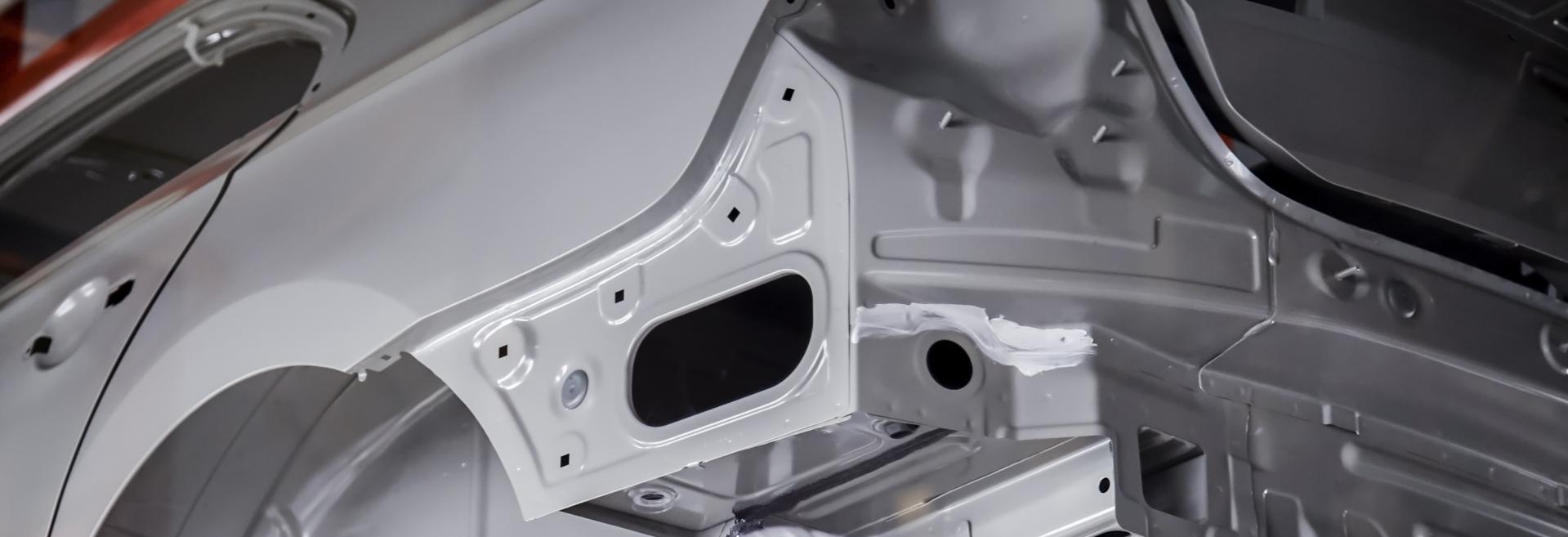
Das Stanzen
Herausforderungen bei der Produktion
Dabei hat Stanzen jedoch einen wesentlichen Nachteil: Mit steigender Blechdicke und/oder steigendem Härtegrad wird es nötig, den Stempel mit immer größerer Kraft zu beaufschlagen, damit er das Material noch durchdringen kann, obwohl er davon stark abgebremst wird. Je dichter der Stempel zur Rückseite des Materials vordringt, desto unvorhersagbarer wird dieser Widerstand. In der Folge kommt es typischerweise zum sogenannten Schnittschlag:
Nachdem der Stempel das Blech fast gänzlich durchdrungen hat, lässt der Widerstand direkt nach, wodurch der Stempel mit viel zu großer Kraft und Tempo weitergleitet. Dies führt dazu, dass an der dem Stempel abgewandten Seite des Werkstücks zu viel Material abgetragen wird.
Daraus ergeben sich mehrere Problemstellungen:
- Ist der Stanzbutzen das gewünschte Element, so hat er an der dem Werkzeug abgewandten Seite einen zu großen und zudem ungleichen Durchmesser. Es ist deshalb nötig, auf Übermaß auszustanzen und durch weitere Bearbeitungsschritte die Schnittkanten wieder zu glätten.
- Ist der Stanzbutzen das Abfallprodukt, so hat das noch eingespannte Blech an den Unterkanten Übermaß und ist ebenfalls ungleich. Entweder muss deshalb dieser Teil wieder aufgefüllt oder der obere Bereich des Stanzlochs erweitert werden.
- Weiter sorgt der Schnittschlag dafür, dass Vibrationen auftreten. Bei den hohen Stanzgeschwindigkeiten in der industriellen Produktion führt dies dazu, dass der Stempel beim Zurückziehen mit den Innenflächen des Bauteils kollidiert, was zu einem übermäßig hohen Verschleiß führt.
Das Risiko für einen Schnittschlag steigt mit Zunahme der Materialstärke und -festigkeit. Abhilfe können jedoch hydraulische Pressen schaffen, die etwa mit einem Servoantrieb gesteuert werden. Dabei lässt sich der Ablauf des Stanzvorgangs präzise regeln und vor der kritischen Schnittphase kurzzeitig abbremsen. So kann der Schnittschlag effizient gedämpft, Lärm und Erschütterungen reduziert sowie die Standzeiten der Anlagen erhöht werden.
Das Feinschneiden
Präzisere Alternative für besondere Anforderungen
Je härter und/oder dicker ein Blech ist, desto weniger präzise und schonend verläuft der Stanzvorgang. Aus diesem Grund hat sich für solche Anwendungen in der jüngeren Vergangenheit das Feinschneiden als Alternative durchgesetzt. Überall dort, wo der Schnittschlag zu einem echten Problem wird, der die Wirtschaftlichkeit der Fertigung beeinträchtigt, kann diese Technik Abhilfe schaffen.
Was die Abläufe der Arbeitsschritte anbelangt, unterscheidet sich das Feinschneiden kaum vom klassischen Stanzen. Dennoch weist es einige wesentliche Unterschiede auf:
- Das Blech wird auf der Oberseite durch die sogenannte Ringzacke eingeklemmt. Dabei handelt es sich um einen formschlüssigen Niederhalter. Das Werkstück wird beim Bearbeiten somit nicht in den Schnittspalt hineingezogen.
- Auf der Unterseite wird ein Gegenstempel eingesetzt. Dieser übt einen kontrollierten Druck auf die Unterseite des künftigen Butzens aus.
Das Material wird durch die Krafteinwirkung des Stempels und die zusätzlichen Sicherungen über den gesamten Kraftwirkungsweg plastisch verformt, bis es durchtrennt ist. Es gibt keinen plötzlichen Materialriss, der Arbeitshub ist deutlich linearer – der Schnittschlag entfällt.
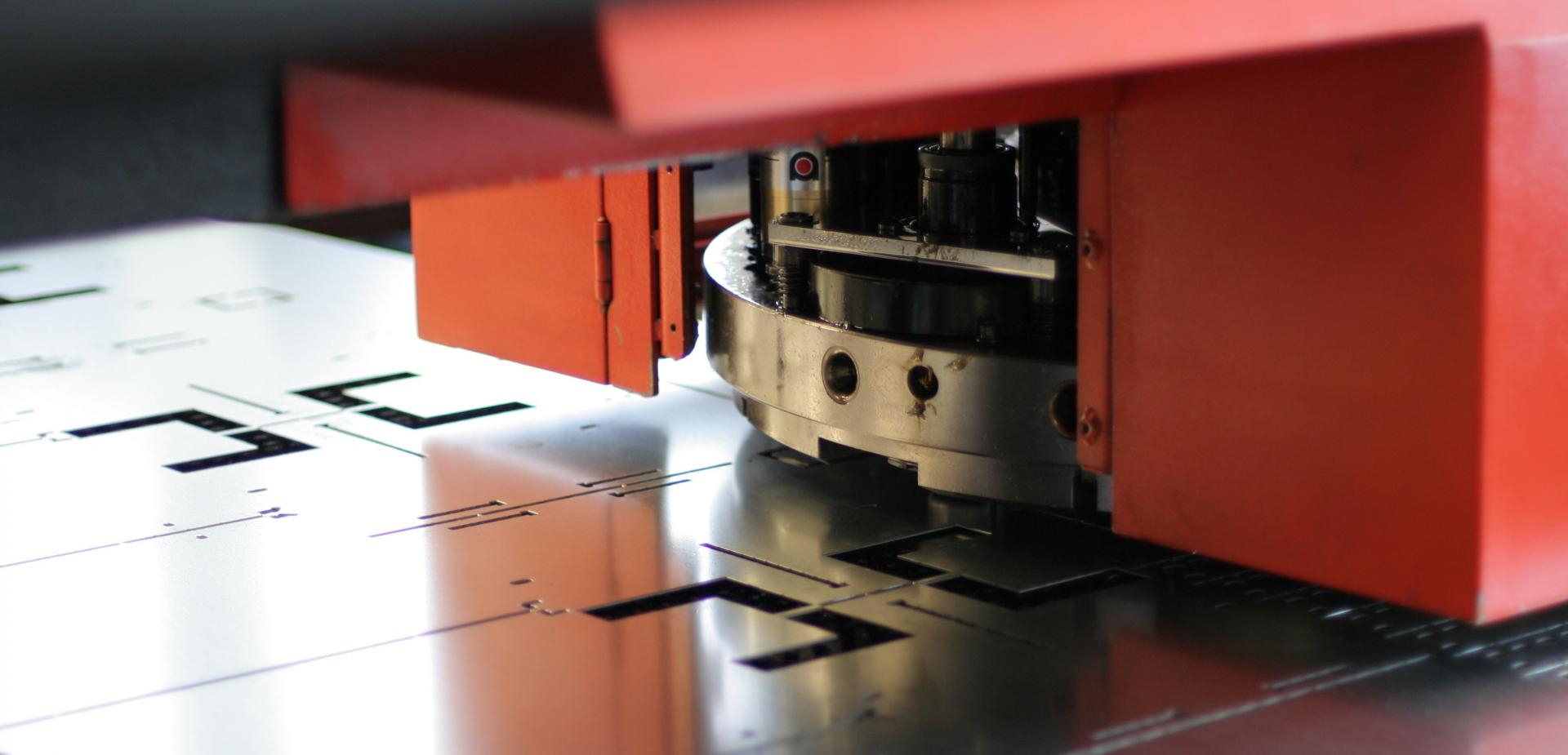
Die drei Abläufe beim Feinschneiden im Überblick:
- Der Schneidstempel wird nach unten durch das Werkstück geführt und kehrt in seine Ausgangsposition zurück.
- Der Niederhalter wird zur Fixierung ebenfalls auf das Werkstück gepresst und gibt es nach dem Bearbeiten wieder frei.
- Für einen präzisen und sauberen Schnitt wird parallel auch der Gegenstempel von unten auf das Werkstück geführt.
Vorteile bei der Produktion
- Die Schnittkanten des Butzens sowie des Ausgangsmaterials sind im Ergebnis kontrolliert maßhaltig und glatt.
- Es sind für viele Anwendungen keine weiteren Nachbearbeitungsschritte mehr vonnöten.
- Die Materialberechnung wird vereinfacht.
- Der Anteil von Abfallmaterial sinkt, was die Produktion ökonomischer macht.
- Dazu lässt sich in einem Arbeitsgang relativ einfach ein Umformungs- oder Prägeschnitt integrieren.
Das Feinschneiden
Komplexe Maschinen für die Produktion
Die höhere Präzision und das Wegfallen des Schnittschlags haben ihren Preis: Feinschneidemaschinen sind aufwendiger und dadurch teurer. Selbst, wenn das Verfahren mittlerweile rund 100 Hübe pro Sekunde erreicht, so ist es doch langsamer als das Stanzen.
Dementsprechend ist Feinschneiden eine Spezialanwendung, die angewendet wird bei:
- großen Blechdicken,
- hohen Härtegraden,
- einer notwendigen hohen Präzision.
Jenseits davon ist klassisches Stanzen die wahrscheinlich ökonomischere Alternative zum spanlosen Zerteilen von Blechen.
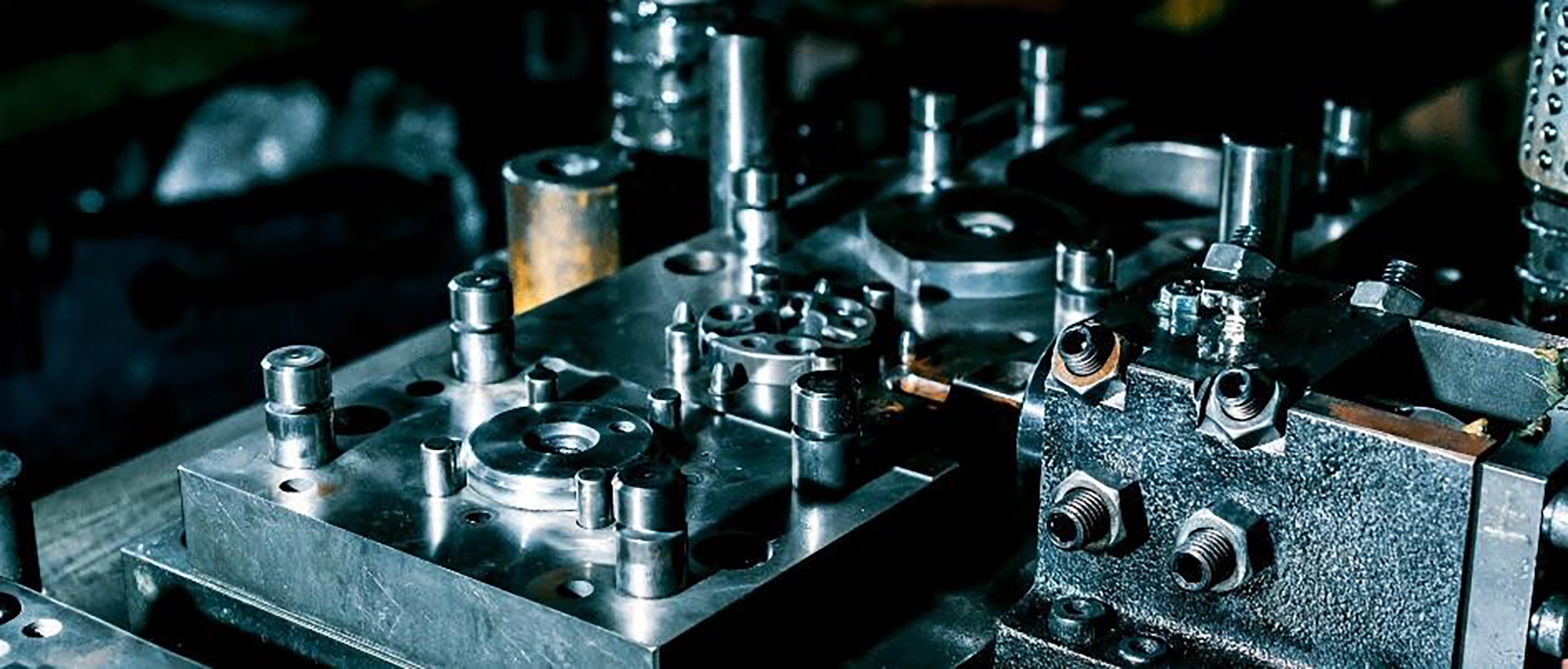
Feinschneiden oder Stanzen?
Beide Verfahren im direkten Vergleich
Die kurze Tabelle zeigt, wo die jeweiligen Schwerpunkte der einzelnen Verfahren liegen:
Stanzen | Feinschneiden |
---|---|
geeignet für sehr hohe Stückzahlen | begrenzte Wirtschaftlichkeit bei höheren Stückzahlen |
geeignet für Bleche bis 24 mm | geeignet für Bleche bis 17 mm |
niedrige Qualitätsanforderungen an die Stanzkontur | hohe Qualitätsanforderungen an die Schneidekontur |
Weitere Verfahren
Laser- und Wasserstrahlschneiden
Weitere Beispiele für spanlose Trennverfahren sind Wasserstrahlschneiden oder auch das thermische Trennen mithilfe eines Lasers oder einer anderen Hitzequelle. Im Rahmen einer industriellen Fertigung sind dafür teilweise komplexe Anlagen notwendig, die eine größere Investition bedeuten.
Diese Verfahren haben in einer industriellen Verarbeitung von Blechteilen und verschiedenen Stahlhalbzeugen eine wichtige Daseinsberechtigung – vor allem dort, wo Material in sehr komplexen und/oder häufig wechselnden Formen bearbeitet werden muss. Dann punkten Laser und Wasserstrahlschneider mit effizienten Abläufen, die sich flexibel an wechselnde Aufgaben anpassen lassen. Die Digitalisierung der Fertigung hat dazu sehr viele vorteilhafte Möglichkeiten eröffnet.
Laserschneiden
Die Vor- und Nachteile
Beim Laserschneiden werden hauptsächlich drei unterschiedliche Verfahren unterschieden:
- Laserstrahlbrennschneiden
- Laserstrahlschmelzschneiden
- Laserstrahlsublimierschneiden
Der Laserstrahl durchtrennt das Material durch seine Hitzeeinwirkung. Während er die notwendige Energie zum Schneiden zur Verfügung stellt, ist dabei zusätzlich ein Gasstrahl notwendig. Meist wird dafür Stickstoff oder Sauerstoff (beim Brennschneiden) eingesetzt. Durch das Gas wird die Schnittfuge ausgeblasen und der Laser geschützt.
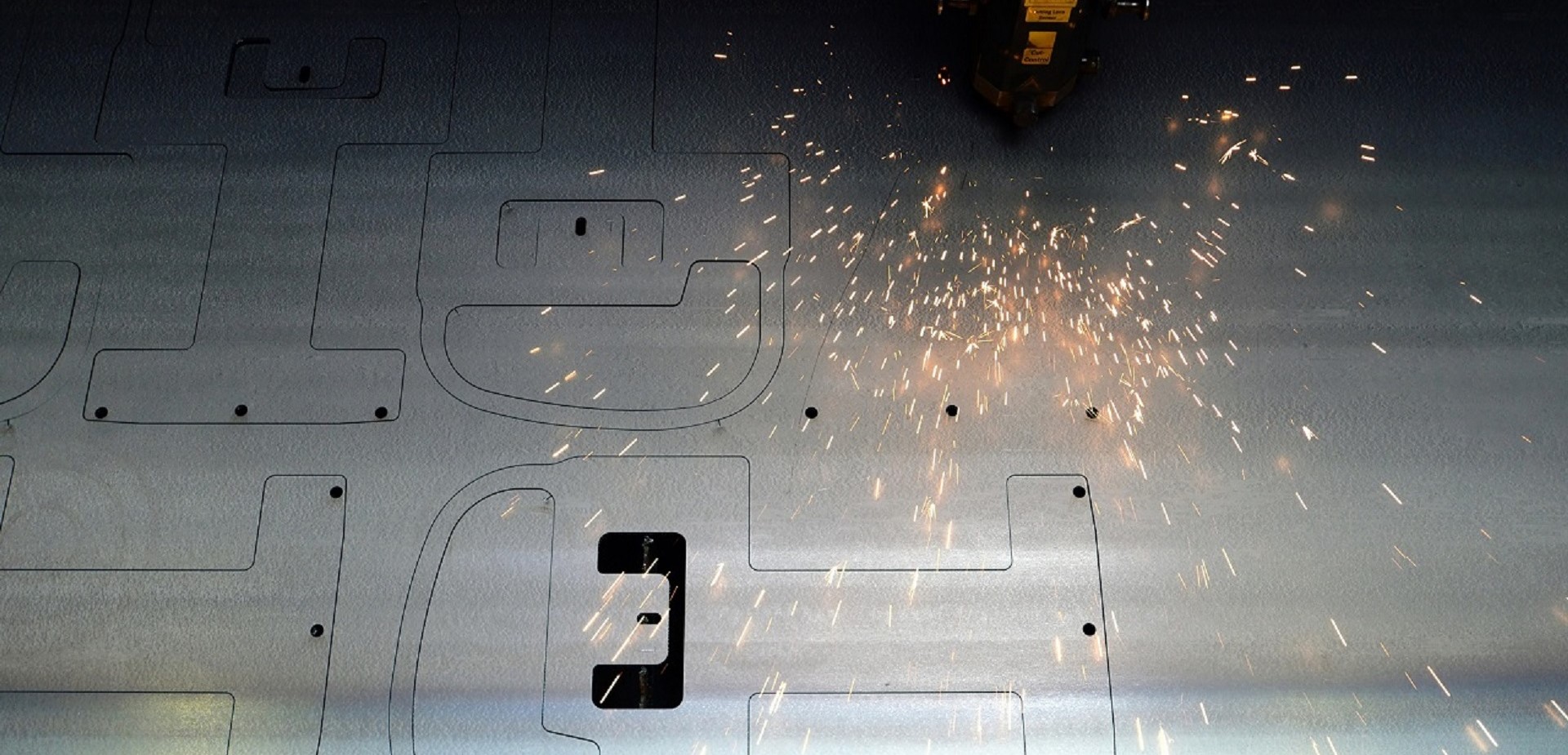
Vorteile | Nachteile |
---|---|
wirtschaftlich ab 1 Stück | hohe Investitionskosten für die Anlage |
effiziente Materialausnutzung | hohe Energiekosten |
schmale Schnittkanten | zusätzliche Kosten für Gas |
meist kein Nachbearbeiten nötig | hohe Anforderungen an Arbeitsschutz |
Wasserstrahlschneiden
Die Vor- und Nachteile
Beim Wasserstrahlschneiden wird das Material entweder durch einen reinen Wasserstrahl oder durch eine Beimischung von abrasiv wirkenden Pulvern zum Schneidestrahl durchtrennt. Möglich wird dies durch einen hohen Schneidedruck, der zwischen 1.000 und 4.000 bar liegen kann. Für Metalle ist ausschließlich das Abrasivschneiden möglich, um das harte Material zu bearbeiten. Auch hier gibt es verschiedene Verfahren:
- Wasser-Abrasiv-Suspensionsstrahlschneiden (WASS): Schneidestrahl besteht aus Wasser und Abrasivmittel
- Wasser-Abrasiv-Injektorstrahlschneiden (WAIS): Schneidestrahl besteht aus Wasser, Abrasivmittel und Luft
Wasserstrahlschneiden eignet sich vor allem für Materialien, die bei Druck- oder Hitzeeinwirkung zu Verformungen neigen. Es lässt sich zudem gerade für größere Materialdicken einsetzen, wo andere Verfahren an ihre Grenzen gelangen. Metalle können in höher Präzision in einer Stärke von bis zu 30 Zentimetern durchtrennt werden. Bei einer geringeren Stärke lassen sich mehrere Werkstücke übereinander anordnen und gleichzeitig bearbeiten.
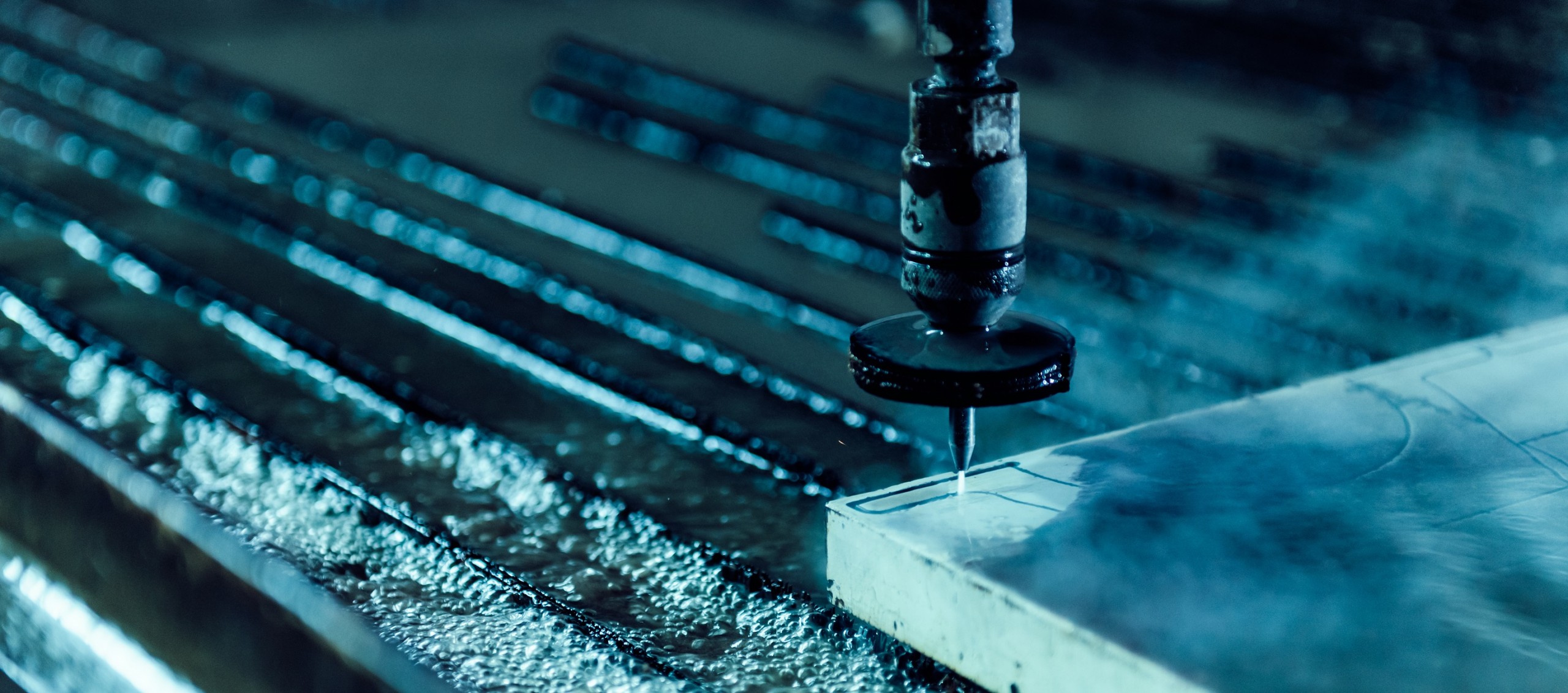
Vorteile | Nachteile |
---|---|
wirtschaftlich ab 1 Stück und ab ca. 15 mm Materialstärke | hohe Investitionskosten für die Anlage |
hochpräzise Schnitte und hohe Qualität der Schnittkanten | zum Teil geringe Schnittgeschwindig-keit für ausreichende Präzision |
Einsatz auch zur Entgratung, Oberflächenreinigung oder zum Abtragen von Material | zusätzlicher Aufwand für Wasserauf-bereitung und Entsorgung von Schlamm |
effiziente Materialausnutzung | Feuchtigkeit und Staub ggf. Problematisch in der Arbeitsumgebung |
Bildquellen:
Bild 1: stock.adobe.com © frog
Bild 2: stock.adobe.com © BigBlueStudio
Bild 3: stock.adobe.com © jeson
Bild 4: stock.adobe.com © Dreef
Bild 5: stock.adobe.com © DRN Studio
Bild 6: stock.adobe.com © industrieblick
Bild 7: stock.adobe.com © kerkezz