Trennen, Verformen, Fügen
Metallrohre werden in unterschiedlichen Materialien angeboten. Die meisten Rohrarten sind in festen Längen und Durchmessern erhältlich – darüber hinaus existieren verschiedene Individuallösungen. Für die Nutzung und Weiterverarbeitung werden dementsprechend ganz unterschiedliche Techniken angewandt. Dazu zählen das Kürzen oder Trennen von Rohrabschnitten, das Verformen einzelner Rohre sowie die Verbindung bzw. das Fügen. Je nach Einsatzzweck stehen teils mehrere Optionen offen.
Die wichtigsten Metalle für die Rohrfertigung
Im Prinzip können Rohre aus jedem Metall bestehen, das auch für andere Metallbauteile genutzt wird. Allerdings ist der primäre Einsatzbereich von Metallrohren auf eine konkrete Bandbreite an Anwendungen beschränkt:
- Transport von Flüssigkeiten und Gasen
- zusätzlicher Schutz von Leitungen
- Konstruktion metallischer Bauteile, etwa Fahrradrahmen
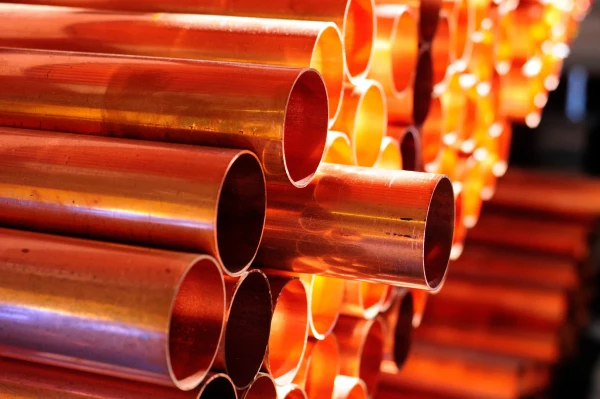
- herkömmliche Stähle,
- (rostträge) Edelstähle,
- Titanlegierungen,
- Aluminiumlegierungen sowie
- Messing und Kupfer.
Bleirohre erkennen – etwa in Altbauten
Bleirohre lassen sich an einer mattgrauen Farbe der oxidierten Oberfläche erkennen. Wird diese auch nur leicht mit anderen metallischen Gegenständen angeritzt, zeigen sich sofort glänzend schimmernde Kratzer. Mit etwas mehr Kraft lassen sich sogar Späne abschaben, da das Material sehr weich ist.
Weitere Gewissheit gibt ein Blick auf die Verbindungsstellen zweier Rohre. Diese sind typischerweise konisch und auf einfachste Art miteinander verpresst. Zusätzliche Hinweise sind frei gebogene Radien, da sich das Material einfach und sogar händisch biegen lässt – im Gegensatz zu den meisten anderen Rohrmaterialien.
Metallrohrverarbeitung I: Trennen
Aufgrund der meist vorkonfektionierten Längen müssen Metallrohre bei der Weiterverarbeitung oft abgelängt werden. Hierfür stehen mehrere Optionen zur Verfügung – je nach Metall und erforderlicher Genauigkeit beim Einhalten eines exakt winklig zum Rohr verlaufenden Schnitts.
Neben einem eher unpräzisen Ablängen mit manuellen Metallsägen, Winkelschleifern sowie Band-, Kreis- und händisch geführten Säbelsägen kommen insbesondere bei der professionellen Bearbeitung spezialisierte Werkzeuge zum Einsatz.
Manuelle Rohrschneider
Dieses Handwerkzeug ermöglicht ein flexibles Vorgehen. In der Praxis ist seine Anwendung aufgrund der Bauweise jedoch auf Rohre mit einem Maximaldurchmesser von etwa 100 mm beschränkt.
Das Werkzeug ähnelt einer verstellbaren Schraubzwinge. An der Spitze eines der Träger sind Rollen integriert. Der andere Träger ist für eine Anpassung an den Rohrdurchmesser verstellbar und mit einem metallischen Schneidrad versehen.
Bei der Anwendung wird der Rohrschneider über das Metallrohr geschoben und an den Durchmesser angepasst. Beim radialen Drehen um das Rohr dringt das Schneidrad in die Rohroberfläche ein. Nach einigen Umdrehungen erfolgt ein Nachjustieren. Auf diese Weise schneidet sich das Rad immer tiefer ins Metall, bis die Rohrwandung durchtrennt wurde.
Manuelle Kettenrohrschneider
Hinsichtlich der Funktion ähnelt dieses Handwerkzeug dem herkömmlichen Rohrschneider. Anstelle des einzelnen Schenkels mit nur einem Schneidrad tritt jedoch eine vielgliedrige Kette, die mit mehreren Schneidrädern ausgestattet ist und sich über Querstifte variabel in den gegenüberliegenden Werkzeugschenkel einhängen lässt.
Häufig ähnelt der Kettenrohrschneider deshalb im Grundaufbau einer feststell- und fein einstellbaren Gripzange. Das Design hat mehrere Vorteile:
- Es können aufgrund der langen Kette deutlich größere Rohrdurchmesser geschnitten werden.
- Durch die vielen gleichzeitig arbeitenden Schneidräder ist es nicht nötig, das Werkzeug im Vollkreis um das Rohr zu bewegen. Dadurch können Kettenrohrschneider gut an beengten Stellen eingesetzt werden.
Angetriebene Rohrsägen
Hierunter fallen verschiedene Bauformen von händisch gehaltenen oder stationären Sägen. Sie können beispielsweise Kreis- bzw. Tauchsägen oder Säbelsägen ähneln. Teilweise handelt es sich sogar nur um Aufsätze für die herkömmlichen Varianten dieser Werkzeuge. Ein Plus ist hier die Möglichkeit, dass ein Rohr in weiteren Winkeln jenseits der 90 Grad durchtrennt werden kann.
Drehbänke, Fräsmaschinen und Plasmaschneider
Die bislang vorgestellten Methoden haben ein breites Einsatzspektrum. Insbesondere bei der industriellen Verarbeitung können sie jedoch zu langsam und/oder nicht präzise genug sein.
Nicht zuletzt gibt es Metallrohre besonders großer Wandstärken oder solche, bei denen ein Bedarf an sehr speziell geformten Schnittkantenprofilen besteht. In diesem Fall können verschiedene Arten von Drehbänken und (computergesteuerten) Fräsmaschinen oder Plasmaschneider die komplexe Arbeit übernehmen.
Hierbei kommen sowohl Methoden zum Einsatz, bei denen das Rohr rotiert und das Werkzeug stillsteht als auch solche, bei denen das Werkzeug radial und axial um das stillstehende Rohr herumbewegt wird.
Metallrohrverarbeitung II: Verformen
Metallrohre sind meist gerade und haben einen über den kompletten Verlauf gleichbleibenden Durchmesser. Sowohl für das Verbinden als auch das Anpassen an eine gewünschte Endform der Konstruktion kann es deshalb erforderlich sein, Rohre zu verformen.
Bördeln
Selbst, wenn zwei präzise abgelängte Rohrstücke mit den Stirnseiten aneinanderstoßen, lässt sich nur auf Umwegen eine Abdichtung erzielen – etwa unter Verwendung zusätzlicher Dichtungselemente, um selbst kleinste Unebenheiten auszugleichen. Auch dann ist noch eine weitere Technik vonnöten, um die Rohre auf die gewünschte Weise zu verbinden.
Insbesondere dort, wo Rohre hohen Druck übertragen müssen, speziell bei Hydraulikleitungen, kommt das Bördeln zum Einsatz. Dabei werden die Rohrenden durch ein entsprechendes Bördelwerkzeug (und meist in kaltem Zustand) durch gezielte Aufweitung und Formgebung plastisch verformt.
Dies hat drei Vorteile:
- Es lassen sich Überwurfschrauben und -muttern einsetzen. Durch die Aufweitung der Rohrenden können diese nach dem Verschrauben nicht mehr verrutschen. Gleichzeitig bleibt diese Verbindung auf einfache Weise lösbar.
- Die Auflagefläche der Stirnseiten wird vergrößert, wodurch die Stabilität der Verbindung erhöht wird.
- Zusätzlich trägt eine gezielte Formgebung dazu bei, dass die Verbindung hohen Druck aushält und sich leicht abdichten lässt. Meist wird ein Rohrende konvex, das andere konkav gebördelt.
Typischerweise werden vor allem Aluminium- und Messing- bzw. Kupferrohre auf diese Weise verformt. Allerdings gibt es im Bereich der mechanischen Optionen ebenso Möglichkeiten, um Stahl- und Titanrohre zu bördeln.
Aushalsen
Für verschiedene Einsatzzwecke ist es notwendig, Metallrohre mit Abzweigungen zu versehen – teilweise sogar, nachdem die Rohre verlegt oder installiert wurden. Eine typische Vorgehensweise wäre es, das Rohr an der entsprechenden Stelle zu durchtrennen, beide Enden zu kürzen und im freigewordenen Raum ein Zwischenstück mit integrierter Abzweigung zu setzen. Das allerdings ist nicht immer möglich.
In solchen Fällen kommt das Aushalsen zum Einsatz. Dabei handelt es sich um eine Technik, die ohne Hinzugabe von weiterem Material, allein durch Umformen, eine aus dem Rohr herauskragende Abzweigung inklusive eines kurzen Ansatzstücks produziert.
Dazu wird – vereinfacht gesprochen – zunächst ein dünnes Loch in die Rohrwandung gesetzt. Dort hinein greifen nacheinander mehrere abgestufte Werkzeuge, die das Loch immer stärker aufweiten und gleichzeitig den Rand nach außen ziehen. Stück für Stück entsteht so ein nahtloser kleiner Rohransatz, der komplett aus der Rohrwand herausgetrieben wurde. Speziell der finnische Hersteller T-Drill hat dieses Verfahren durch patentierte Werkzeuge revolutioniert, da bei seiner gleichnamigen Technik lediglich noch drei Fertigungsstufen nötig sind – wo es zuvor deutlich mehr waren.
Biegen
Ganz ähnlich wie beim Erstellen von Abzweigungen wird auch das Anfertigen von Metallrohren mit Winkeln <180° häufig mit entsprechenden Verbinderstücken durchgeführt.
Die Herausforderungen:
- Verbindungsstücke sind meist nur in typischen Winkeln wie 22,5°, 45°, 90° usw. erhältlich. Diese passen für viele Situationen, aber nicht für alle.
- Insbesondere bei komplexeren Biegesituationen kann die Aneinanderreihung mehrerer Verbinderstücke eine zu teure und komplexe Herangehensweise sein.
Dementsprechend ist das Biegen von Metallrohren, speziell bei benötigten Freiformen und weiten Biegeradien, die oftmals bessere Wahl.
Die Schwierigkeit besteht jedoch im Hohlprofil der Rohre in Verbindung mit der hohen Materialhärte. So besteht zwischen dem Material der Kurvenaußen- und -innenseite ein großer, luftgefüllter Abstand. Ohne passende Methoden wird jedes Rohr bei herkömmlichen Biegeversuchen im Scheitelpunkt des Biegeradius knicken – außer Bleirohre und einige spezielle Kupferrohre. Das kreisrunde Rohrprofil wird an dieser Stelle zusammengedrückt, dieses Rohr kann nicht mehr verwendet werden.
Um Metallrohre zu biegen, muss deshalb mehr Aufwand betrieben werden als beim Verformen anderer Metallprofile.
- Manuell: Das Rohrstück wird mit einem rieselfähigen, wärmeunempfindlichen Material gefüllt (etwa Sand oder Korund) und dieses anschließend verdichtet. Dann wird das Rohr an beiden Enden verschlossen. Der zu biegende Bereich wird, beispielsweise durch einen Gasbrenner, erhitzt, bis die Solidustemperatur überschritten ist. Dann lässt sich das Rohr über eine entsprechende Matrize biegen. Da das Füllmaterial aufgrund der verschlossenen Enden nicht ausweichen kann, übt es einen Gegendruck aus, der ein Knicken effektiv verhindert.
- Mechanisch: Es kommen händische oder angetriebene Rohrbieger zum Einsatz. Diese üben durch speziell geformte Halterungen und Mechaniken einen über ein längeres Rohrstück gleichmäßigen Druck aus. Auf diese Weise wird ein Knicken ebenfalls verhindert. Zudem wird das Metall nicht durch das Erhitzen belastet.
Metallrohrverarbeitung III: Fügen
Verschrauben mit Muffen
Verschiedene Rohre weisen eine im Vergleich zum Durchmesser große Wandstärke auf. Sie lassen sich mit entsprechenden manuellen oder mechanischen Maßnahmen leicht mit einem Außengewinde versehen. Als verbindendes Element kommt eine Muffe zum Einsatz – eine Art verlängerte Mutter. Sie enthält das passende Innengewinde. Zunächst wird die Muffe auf das eine Rohr geschraubt, dann wird das andere Rohr in diese Muffe hineingedreht.
Wo Rohrverbindungen nochmals im verbauten Zustand gelöst werden müssen, können Rohre und Muffen mit kombiniertem Rechts- und Linksgewinde genutzt werden. Damit wird es durch Drehen der Muffe möglich, beide Rohre gleichzeitig festzuziehen oder zu lösen. Wird diese Verbindungsart bei Rohrleitungen zum Transport von Gasen oder Flüssigkeiten eingesetzt, muss das Gewinde zusätzlich abgedichtet werden. Heute geschieht dies entweder mit speziellen Dichtungsflüssigkeiten oder Teflonbändern.
Löten und Schweißen
Eine spätere Lösbarkeit ist bei vielen Rohrverbindungen von nachrangiger Bedeutung. Für bestimmte Einsatzzwecke ist jedoch eine selbst unter Extrembedingungen gewährleistete Dichtigkeit und mechanische Stabilität absolut maßgeblich – beispielsweise bei Pipelines für Gas oder Wasser. Hier sind das Löten oder Schweißen von Rohrverbindungen nach wie vor die beiden wichtigsten Methoden. Wie sie sich im Detail voneinander unterscheiden, haben wir bereits in einem eigenen Artikel detailliert erläutert.
Daher an dieser Stelle nur die wichtigsten Unterschiede:
- Beim Löten werden Metalle durch die erreichten Temperaturen höchstens weich, jedoch nie flüssig. Deshalb ist ein Lot als Hilfsfügematerial notwendig. Es geht mit der Rohroberfläche (jedoch nur mit dieser) eine Legierungs-artige Verbindung ein.
- Schweißen hingegen verflüssigt beide Rohrenden, sodass sie selbst auf molekularer Ebene zu einem einzigen Gefüge werden. Je nach Schweißtechnik kommt dabei ebenfalls ein Hilfsfügematerial zum Einsatz – muss es aber nicht.
Insbesondere beim Löten werden jedoch die Rohrenden typischerweise nicht einfach nur an den Stößen verlötet, das wäre mitunter nicht belastbar genug. Häufig werden deshalb entweder aufzuschiebende Muffen verwendet oder ein Rohrende wird durch Bördeln aufgebogen, damit es sich über das andere Rohrende schieben lässt.
Verschrauben mit Klemmverbindern
Eine weitere Fügemethode, speziell bei Stahlrohren zur Beförderung von Gasen und Flüssigkeiten, sind Klemmverbinder. Hierbei ist zur Vorbereitung nichts weiter zu tun, als zwei Rohrenden sauber zu entgraten.
Dann kommt ein spezieller Klemmverbinder zum Einsatz. Beim Verschrauben presst er sich um die Rohroberfläche und dichtet die Verbindung ab (Die Wirkungsweise ist grob mit Wasserschlauchverbindern vergleichbar). Da dies auf beiden Seiten geschieht, lassen sich sowohl Rohrverbindungen als auch Abzweigungen schnell und unkompliziert aufbauen, solange es rings um das Rohr genügend Raum für den Klemmverbinder gibt.
Verpressen mit und ohne Pressfittings
Dünnwandige Rohre, etwa solche aus Messing, können nicht mit einem Gewinde versehen werden, ohne die Wandstärke zu stark zu schwächen. Hier können Pressfittings genutzt werden. Die speziell geformten Hülsen werden über das Rohr geschoben und dann mit Spezialwerkzeugen axial zusammengepresst. Dabei werden beide Elemente so stark miteinander verpresst, dass eine hermetisch abgedichtete Verbindung entsteht.
Ohne eine zusätzliche Hülse werden die Rohrenden in mehreren Arbeitsschritten mit Spezialwerkzeugen aufgeweitet und auf eine Weise umgebördelt, durch die eine Haken-ähnliche Formgebung entsteht. Dann lassen sich beide Rohre zusammenschieben und verpressen damit eine ähnlich stabile Verbindung entsteht.
Bildquellen:
Bild 1: stock.adobe.com © stetsko
Bild 2: stock.adobe.com © Windsor
Bild 3: stock.adobe.com © Ocskay Mark
Bild 4: stock.adobe.com © Michal
Bild 5: stock.adobe.com © thomsond
Bild 6: stock.adobe.com © Thaweesak
Bild 7: stock.adobe.com © g0d4ather
Bild 8: stock.adobe.com © hodim
Bild 9: stock.adobe.com © Nikolay
Bild 10: stock.adobe.com © Ingo Bartussek
Bild 11: stock.adobe.com © OlegDoroshin