Wie Normen und Prüfverfahren Qualität sicherstellen
Ob Werkzeuge, Maschinen, Gebäude oder Brücken, vieles in unserer Welt wird aus Metall gebaut – vor allem dann, wenn Robustheit und Langlebigkeit gefragt sind. Häufig kommt dabei Stahl zum Einsatz. Ein Metall, das elastisch und formbar, doch auch stabil und widerstandsfähig ist. Doch ebenso wichtig ist die Qualität des Stahls – und diese wird durch Normen und Prüfungen gesichert.
Facettenreiches Metall
Stahl ist nicht gleich Stahl
Als Werkstoff begleitet Stahl uns Menschen schon lange Zeit, insbesondere in Form von Werkzeugen und Waffen. Doch über die Jahrhunderte und mit der Entwicklung moderner Technologien, wie etwa des Hochofens, offenbarte sich schnell das Potential der vielseitig nutzbaren Eisen-Kohlenstoff-Legierung.
So versteckt sich hinter dem Begriff Stahl heute sehr viel mehr als bloß ein Metall: Rund 2500 Stahlsorten sind mittlerweile genormt – und jeder einzelne dieser Stähle ist mit Blick auf seine Herstellung, Beschaffenheit und Eigenschaften ganz und gar einzigartig.
Das Sortenreichtum hat seinen guten Grund: Jeder Einsatzbereich eines Werkstoffs birgt spezifische Anforderungen. Stahl, der Brücken tragen soll, ist mit anderen Ansprüchen und Belastungen konfrontiert als ein Zahnrad, das sich unentwegt in einer Maschine dreht.
Daher ist die Werkstoffwahl für Ingenieure oder Konstrukteure eine äußerst heikle Angelegenheit; Fehler sind hier tabu. Um sicherzustellen, dass das bestgeeignete Material zum Einsatz kommt, braucht es deshalb zuverlässige Standards, an denen sich Hersteller und Abnehmer orientieren können, sprich Normen.
Werkstoffnormung
Ziele und Zwecke von Normen
Unsere Welt wird immer komplexer – und davon ist auch die Produktion, Verarbeitung und der Handel mit Werkstoffen nicht ausgenommen. Stetig werden neue Materialien entwickelt. Gleichzeitig sorgt die Globalisierung für einen immer besser vernetzten, aber unübersichtlichen Weltmarkt. Aus diesem Grund nehmen sich sowohl auf nationaler als auch auf internationaler Ebene zahlreiche Organisationen der Aufgabe an, Normen zu erstellen, die als Orientierungshilfe dienen. Denn Normen bekunden nicht nur einen gewissen Qualitätsstandard, sie machen Werkstoffe und Produkte zugleich vergleichbar.
Normen erleichtern somit die Zusammenarbeit und Verständigung in der globalen Wirtschaft, Wissenschaft und Öffentlichkeit. Doch das ist nur ein Grund von vielen, der die oft bürokratisch anmutende Normung für unsere Gesellschaft unverzichtbar macht.
Vorteile von Normen:
- Sicherung von Qualität und Produktsicherheit
- Schutz der Umwelt und Verbrauchergesundheit
- Vereinfachung interner und externer Unternehmenskommunikation
- Entscheidungshilfe für Konstrukteure bei der Werkstoffauswahl
- Förderung von Produktivität und Innovation
- Vereinheitlichung von Produktionsverfahren – für vergleichbare Ergebnisse, unabhängig vom Hersteller
Gesetzlich verpflichtend sind Normen allerdings nicht. Die Einhaltung beruht also auf Freiwilligkeit. Denn bei Normen handelt es sich vielmehr um unverbindliche Empfehlungen und Vereinbarungen als um Gesetze. Bindend sind diese nur, wenn sie vertraglich festgehalten wurden, zum Beispiel in einem Kaufvertrag.
Wichtige Normungsinstitute
Normen für Deutschland, Europa und die Welt
Die hierzulande wichtigste Organisation für Normungen ist das Deutsche Institut für Norm e.V. (DIN). Diese erstellt, pflegt und veröffentlicht den deutschen Normenkatalog. Auch der Verein Deutscher Ingenieure (VDI) erstellt Normen und Richtlinien für Stahl, mit Fokus auf dem Maschinenbau.
Ebenso relevant sind Europäische Normen (EN). Dabei handelt es sich um international gültige Normen, die in Zusammenarbeit mehrerer europäischer Institute erstellt werden. Das Ziel dabei ist, auf dem europäischen Markt einheitliche Standards zu schaffen, die etwa auch von der Internationalen Organisation für Normung (ISO) global verfolgt werden. So ist die ISO zuständig für Normungen in mehr als 100 Staaten.
Weitere wichtige (obwohl nationale) Normen für Stahlbranche hierzulande sind etwa die ANSI- und JIS-Normen aus den USA beziehungsweise Japan – besonders die amerikanischen ANSI-Normen werden oftmals (zusätzlich zur DIN und EN) angeführt.
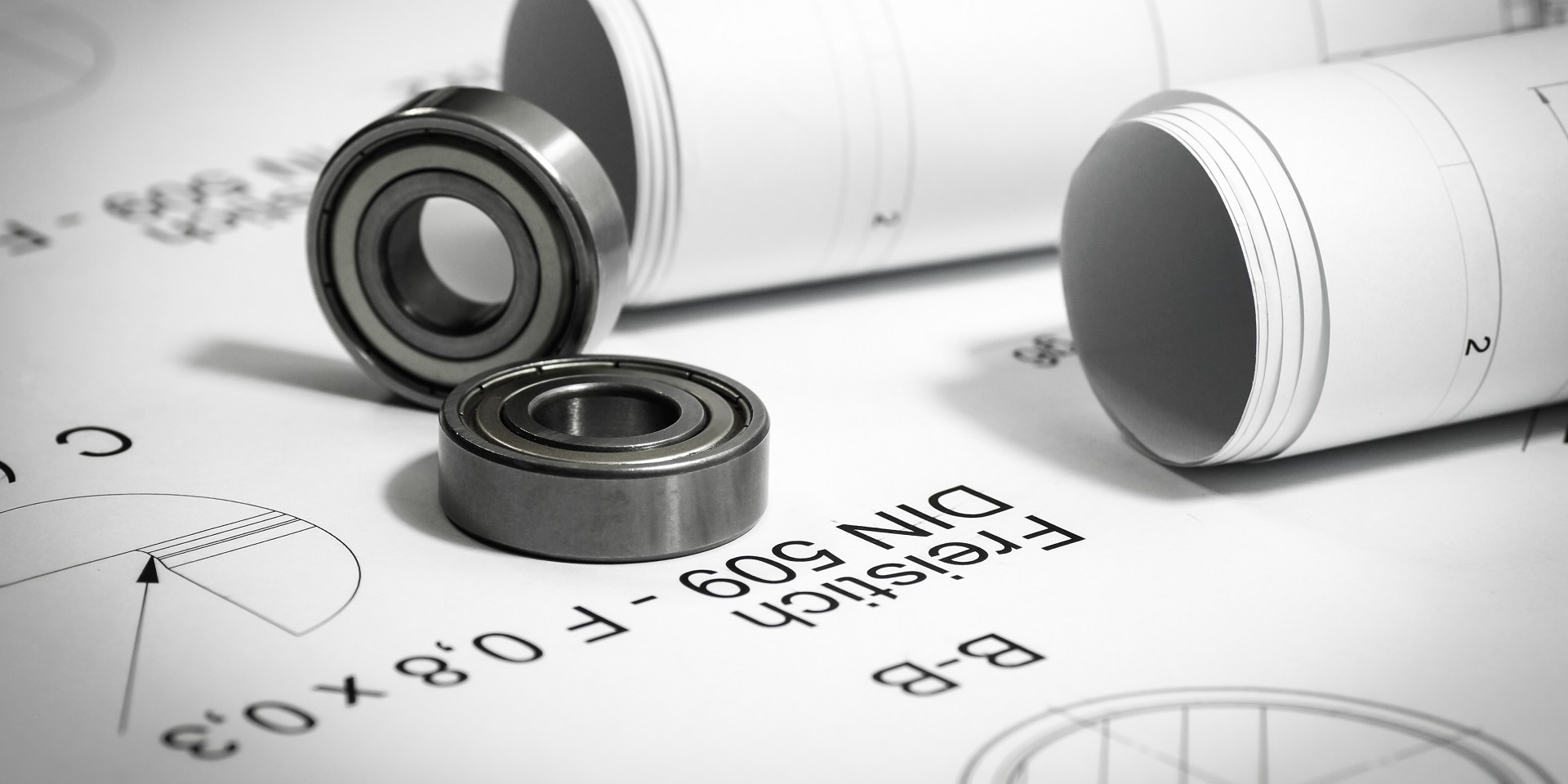
Klassifizierung durch Stahlnormen
Güteklassen, Werkstoffnummern und Kurznamen
Stahlnormen können als Ordnungssysteme verstanden werden, die dazu dienen, Stahlsorten anhand ihrer chemischen, mechanischen und metallurgischen Eigenschaften zu klassifizieren, beurteilen und spezifizieren. Für die Normung können also diverse Kriterien herangezogen werden.
Relevante Kriterien für die Normung von Stahl:
- die chemische Zusammensetzung der Legierung
- das Herstellungsverfahren (z. B. Herdofen, Elektrolichtbogenofen)
- Umformungsmethode, Oberflächenvergütung und Plattierungstechnik
- Produktform (z. B. Bandstahl oder Bleche, Stäbe und Rohre)
- Mikrostruktur (z. B. ferritisch, perlitisch oder martensitisch)
- Wärmebehandlung (z. B. Glühen, Abschrecken, Anlassen)
Eine der grundlegenden Stahl-Normen betrifft die Einteilung von Stahl in die verschiedenen Güteklassen. Diese ist in der DIN EN 10020 verankert. Darin wird Stahl grob nach seiner chemischen Zusammensetzung in die entsprechenden Hauptgüteklassen eingeteilt:
- Unlegierte Stähle
sind Stahlsorten, bei denen die Anteile gewisser (rund 20) Elemente nicht über einem bestimmten Grenzwert liegen.
Zudem wird in dieser Güteklasse zwischen unlegierten Qualitäts- beziehungsweise Edelstählen unterschieden.
- Legierte Stähle
sind Stahlsorten, die diverse Anforderungen in Bezug auf Zähigkeit, Korngröße und Umformbarkeit erfüllen.
Auch in dieser Güteklasse wird zwischen (legierten) Qualitäts- und Edelstählen differenziert.
- Rostfreie Stähle
verfügen über einen maximal 10,5 Prozent hohen Masseanteil Chrom und einen Anteil von höchstens 1,2 Prozent Kohlestoff.
Weiter unterschieden wird in dieser Gruppe nach Nickelgehalt, Warmfestigkeit sowie der Korrosions- und Hitzebeständigkeit.
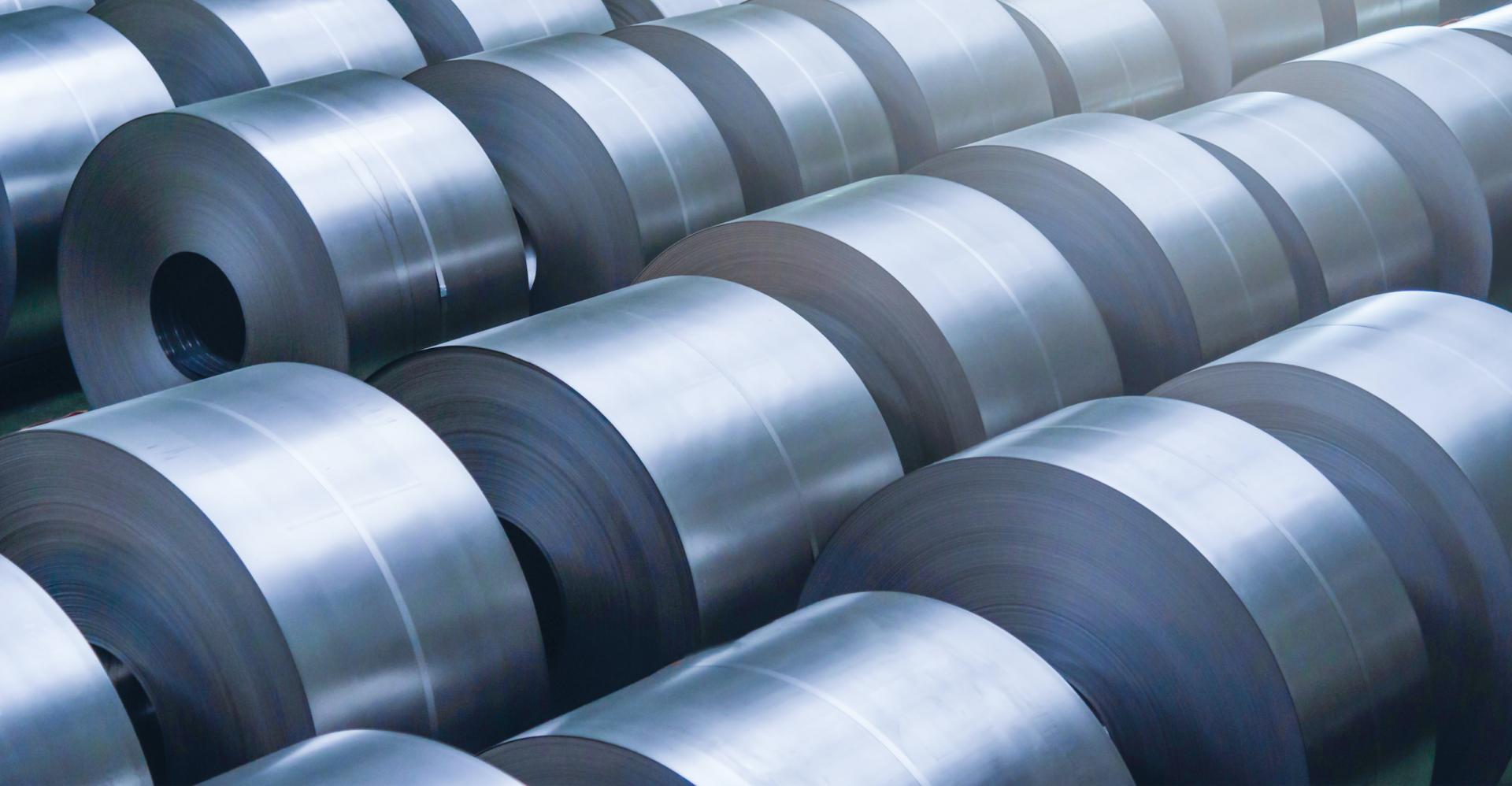
Die Bezeichnung einzelner Stahlsorten, die innerhalb einer der oben genannten Hauptgüteklassen fallen, wird ebenfalls genormt – zum Beispiel in Form von Werkstoffnummern und Werkstoffkurznamen:
- Werkstoffnummern für Stähle
werden als fünf- bis siebenstellige Ziffernreihen dargestellt, wie zum Beispiel 1.2345(67). Die erste Ziffer steht dabei für die Werkstoff-Hautgruppe, welche im Falle von Stahl immer 1 lautet.
Danach folgt eine zweistellige Stahlgruppennummer sowie eine zweistellige Zählnummer, welche die einzelnen Stahlsorten durchnummeriert. Je nach Anzahl von Stählen innerhalb einer Gruppe, kann die Zählernummer auch vier Stellen umfassen.
- Werkstoffkurznamen für Stähle
richten sich nach dem jeweiligen Einsatzbereich des Stahls. Die Namen setzen sich aus mehreren Zeichen zusammen. Der erste Buchstabe gibt Aufschluss über den Hauptanwendungsbereich.
„S“ steht etwa für Stahlbau, „B“ für Betonstahl. Bei Stahlguss wird diesen noch ein „G“ vorangestellt. Im Anschluss folgen Buchstaben, Symbole und Werte, die nähere Informationen zu den mechanischen und physikalischen Eigenschaften des Stahls geben.
Die Werkstoffprüfung
Metall auf dem Prüfstand
Normungen allein gewährleisten Qualitätssicherung nur bedingt. Als zweites, Instrument kommt deshalb die Werkstoffprüfung ins Spiel. Im Rahmen dieser werden Werkstoffe je nach Verfahren mithilfe von mechanischen, thermischen oder chemischen Beanspruchungen hinsichtlich ihres Verhaltens und ihrer Eigenschaften geprüft.
Grundsätzlich kann zwischen der zerstörenden und der zerstörungsfreien Werkstoffprüfung unterschieden werden. Der aufgrund des Namens offensichtlichste Unterschied besteht darin, dass die Proben je nach Prüfart beschädigt werden oder unversehrt bleiben.
Wer führt Werkstoffprüfungen durch?
- Zu den wichtigsten Organisationen für Werkstoffprüfung zählt die Bundesanstalt für Materialforschung und -prüfung (BAM).
- Es gibt aber auch privatwirtschaftliche Prüforganisationen. Diese sind in der Fachgesellschaft der akkreditierten Prüfgesellschaft (F-GZP) organisiert.
- Ebenso führen etwa der TÜV und das Fraunhofer-Institut für zerstörungsfreie Prüfverfahren Werkstoffprüfungen durch.
Die beiden Prüfungsarten unterscheiden sich zudem hinsichtlich ihrer Einsatzbereiche. Die Verfahren der zerstörenden Werkstoffprüfung kommen vorrangig zum Einsatz, um Werkstoffkennwerte zu ermitteln, wie zum Beispiel:
- Festigkeits- und Verformungseigenschaften
- Zähigkeitseigenschaften
- technologische Eigenschaften
Werte wie diese können mit der zerstörungsfreien Werkstoffprüfung nicht ermittelt werden. Stattdessen wird diese angewandt, um beispielsweise fertige Bauteile zu untersuchen, ohne diese unbrauchbar zu machen und somit weiterverwenden zu können – zumindest, sofern keine Mängel beanstandet werden.
Deshalb kommen zerstörungsfreie Verfahren vor allem bei Inspektionen zum Einsatz, etwa um Oberflächen und/oder Innenfehler zu lokalisieren. Das Ergebnis der zerstörungsfreien Werkstoffprüfung ist somit meist eine Aussage über die weitere Einsatzfähigkeit eines Bauteils.
Beispiele Prüfverfahren
Zerstörende Werkstoffprüfung
Mit dem Zugversuch werden Festigkeit und Zähigkeit eines Werkstoffs ermittelt. Dabei wird eine Werkstoffprobe bei stetig zunehmender (quasi-statischer) Zugbeanspruchung gereckt. Dadurch wird unter anderem festgestellt, welcher Belastungsintensität das Material standhält, bis es bricht und wie weit sich das Material bis zum Bruch dehnt.
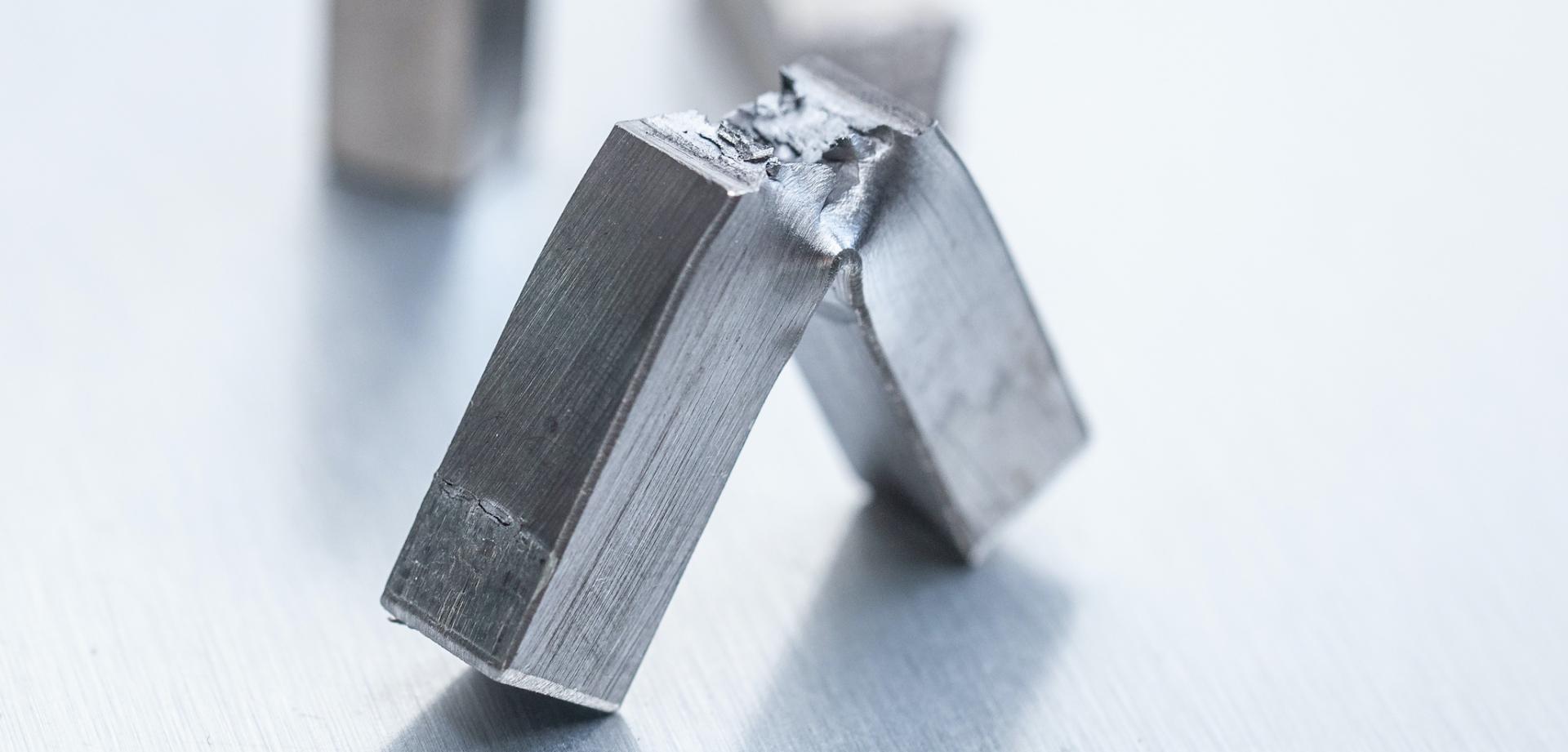
Mit dem Kerbschlagbiegeversuch wird die Zähigkeit geprüft. Anders als beim Zugversuch, werden die Proben hierbei einer stoßartigen Belastung ausgesetzt – üblicherweise bei unterschiedlichen Temperaturen, um realistischere Verhältnisse zu schaffen.
Beim Druckversuch wird die Werkstoffprobe nicht gereckt, sondern bei zunehmender Druckbelastung gestaucht. Dabei wird untersucht, ab welcher Druckbeanspruchung das Material bricht, reißt und sich bleibend verformt.
Der Biegeversuch gibt Aufschluss über das Biegeverhalten von Werkstoffen und wird vor allem bei spröden Werkstoffen, wie es eben auch Stahl ist, eingesetzt. Dabei werden die Probestücke unter Zug- und Druckbelastung bis zum Bruch oder plastischen Verformung gebogen.
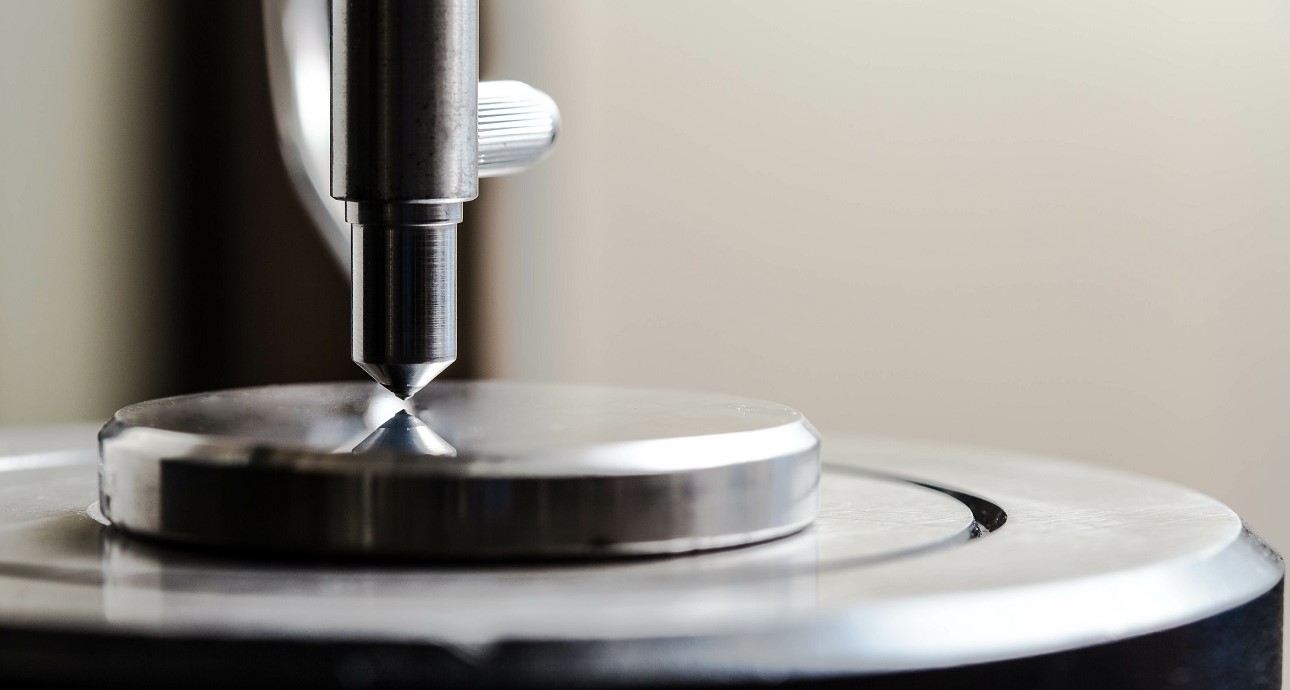
Die Härteprüfung ist ein Prüfungsverfahren, das Rückschlüsse auf die Verschleißfestigkeit eines Werkstoffes erlaubt. Bei der Härteprüfung nach Brinell wird dazu beispielsweise eine Hartmetallkugel bei stetig steigender Kraft in den Werkstoff gedrückt, um so den Widerstand gegenüber dem eindringenden Körper zu messen. Je kleiner die resultierende Druckstelle ausfällt, desto härter ist das Material.
Beim Dauerschwingversuch wird die Festigkeit eines Werkstoffs untersucht. Dabei werden Werkstoffproben oder ganze Bauteile in eine Vorrichtung gespannt, welche sie anschließend per Resonanz in Schwingung versetzt. Dadurch wird das Material wechselnden Belastungsstärken und -Richtungen ausgesetzt, wie es etwa bei Bauteilen wie Zahnrädern und Federn der Fall ist.
Beim Tiefungsversuch wird das Tiefziehverhalten von Blechen untersucht. Bleche für Tiefziehanwendungen müssen stark verformbar und dabei möglichst rissfest sein. Eine Stahlkugel wird in das Blech gedrückt, während dieses von Niederhaltern in Position gehalten wird. Anders als bei der Härteprüfung wölbt sich das Material auf der Rückseite. Je tiefer die Wölbung wird, ohne dass ein Riss entsteht, desto höher ist in der Regel die Tiefziehfähigkeit.
Beispiele Prüfverfahren
Zerstörungsfreie Werkstoffprüfung
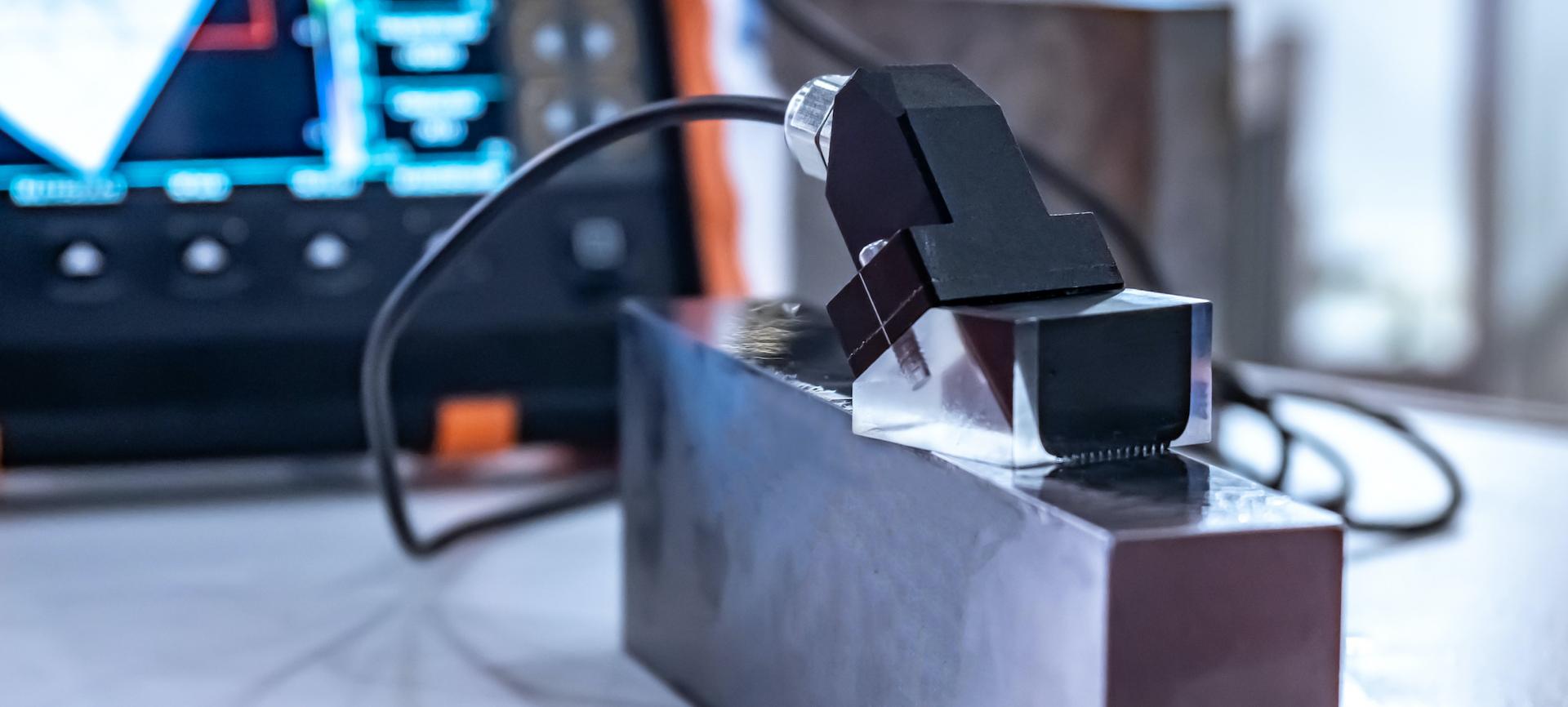
Bei einer Ultraschallprüfung werden Prüfobjekte auf Fehler untersucht, die sich unter der Oberfläche befinden. Die gängigste Form der Ultraschallprüfung ist das Impuls-Echo-Verfahren. Dabei werden akustische Ultraschallwellen impulsartig in das Prüfobjekt gesendet.
Trifft der Schall auf Fehlstellen (zum Beispiel Poren, Lunker und Risse), ändert sich die Ausbreitungsgeschwindigkeit. Dadurch können die Fehler anhand des rückschallenden Echos lokalisiert werden.
Die Röntgenprüfung eignet sich ebenfalls dazu, nicht sichtbare Mängel aufzuspüren. Hierbei wird das Prüfobjekt mit Hilfe von Röntgenstrahlen untersucht. Die Reichweite der Strahlen beträgt bei Stahl rund 300 Millimeter. Während dieses Vorgangs wird die Dichte des Materials auf einem Röntgenfilm festgehalten. Je dicker und dichter das Material ist, desto weniger Strahlen durchdringen es. Auf der Abbildung entstehen dadurch Kontraste, die auf Abweichungen hinweisen.
Die Magnetpulverprüfung eignet sich ausschließlich für die Untersuchung ferromagnetischer Werkstoffe. Der Werkstoff beziehungsweise das Werkstück müssen werden dabei zunächst magnetisiert, wodurch parallel zur Oberfläche verlaufende Feldlinien entstehen. Gibt es im Inneren Fehlstellen wie Risse, bilden sich ein magnetisches Streufeld und Magnetpole. Wird nun Magnetpulver über dem Streufeld verteilt, sammelt es sich an den Fehlstellen.
Das Farbeindringverfahren wurde entwickelt, um Oberflächenfehler sichtbar zu machen. Die gereinigte Oberfläche wird dabei mit einem dünnflüssigen Farbmittel bestrichen, welches durch die Kapillarwirkung in Poren und Risse gezogen wird. Nach einer gewissen Einwirkdauer wird die Oberfläche wieder gereinigt, lediglich die Farbe in den Rissen bleibt. Anschließend wird Entwicklerflüssigkeit aufgetragen, die sich mit der Farbe verbindet und unter ultraviolettem Licht schließlich an den Rissen zum Vorschein kommt.
Bildquellen
Bild 1 © Simone_n, Adobe Stock
Bild 2 © Maksym Yemelyanov, Adobe Stock
Bild 3 © Countrypixel, Adobe Stock
Bild 4 © Nuttawutnuy, Adobe Stock
Bild 5 © Olaf Schwenty, Adobe Stock
Bild 6 © kimtaro2008, Adobe Stock
Bild 7 © Gripb, Adobe Stock