Verschiedene Verfahren im Vergleich
Bei praktisch jedem branchenüblichen Verfahren, das Bleche auf gewünschte Formate und Abmessungen bringt, entstehen an den Schnittkanten Grate. Sie zu entfernen ist bei den meisten Blechprodukten eine bedeutende Notwendigkeit, um ein fertiggestelltes Produkt hoher Güte zu gewährleisten.
Der Grat – Allgemeiner Überblick zur Entstehung
Generell handelt es sich beim Grat lediglich um einen Dachbegriff. Um ihn genauer zu erläutern, ist ein Blick auf den industrialisierten Blechzuschnitt vonnöten. Dabei geht es nicht nur um das Abtrennen von überschüssigem Material, sondern auch darum, eine Schnittkante mit kontrollierter Geometrie zu erzeugen.
Ein Beispiel dafür ist das gängige Stanzverfahren. Ein waagerecht liegendes Blechstück wird von einem senkrecht einlaufenden Stanzmesser durchtrennt. Hier ist es technisch gewünscht, dass die Schnittkante zur Blechober- und -unterseite einen genauen rechten Winkel einhält und dass die Schnittkante über ihre gesamte Länge plan ist – ohne Wellen und ähnliche Fehler.
Der Grat hingegen stellt einen solchen Fehler dar. Seine Definition gemäß DIN ISO 13715:
Grate laut DIN ISO 13715
„Innerhalb der ideal-geometrischen Form einer Werkstück-Außen- oder -Innenkante liegende Abweichung.“
Der Grat besteht bei trennenden Verarbeitungsschritten immer aus Materialanteilen des Werkstücks selbst. Das heißt, er wird nicht durch Fremdquellen auf die Schneidkante aufgebracht. Zudem ist der Grat getrennt von anderen Abweichungen der Form der Schnittkante zu betrachten.
Seine Entstehung ist entweder auf Materialverdrängung oder auf Kantenbildung zurückzuführen. Letzteres kann beispielsweise bei thermischen Fertigungsverfahren geschehen, wenn es zu Schlackebildung kommt. In diesem Fall stellt die Schlacke den Grat dar.
Überdies ist die Art von Graten nicht einheitlich. Sie zeigen sich in drei distinktiven Formen:
- Ausfaserungen
- geometrisch unbestimmte Kanten
- Splitterungen
Der Grund für die Gratentstehung liegt bei der Metallbearbeitung praktisch ausschließlich in der allgemeinen Natur der gewählten Technik des Zuschnitts. Allerdings können Grate auch durch eine nicht perfekt ausgeführte Vorgehensweise entstehen. Etwa beim Laserschnitt, wenn der Laser nicht korrekt fokussiert wurde.
Dabei ist eine Gratentstehung aus physikalischer Sicht bei kaum einem Fertigungsverfahren vermeidbar. Spätestens auf mikroskopischer Ebene zeigt sich praktisch immer ein Grat. Dennoch kann sich das Ausmaß auf technischer Ebene teils erheblich voneinander unterscheiden – in solche, die aufgrund ihres Ausmaßes tatsächlich von Relevanz für das Endergebnis sind und solche, die unter diesem Blickwinkel vernachlässigbar sind.
Trennende Fertigungsverfahren werden deshalb für die praktische Anwendung in gratlose und gratbehaftete Verfahren unterteilt. Der Unterschied liegt in diesem Fall lediglich im prozentualen Anteil der Gratbildung.
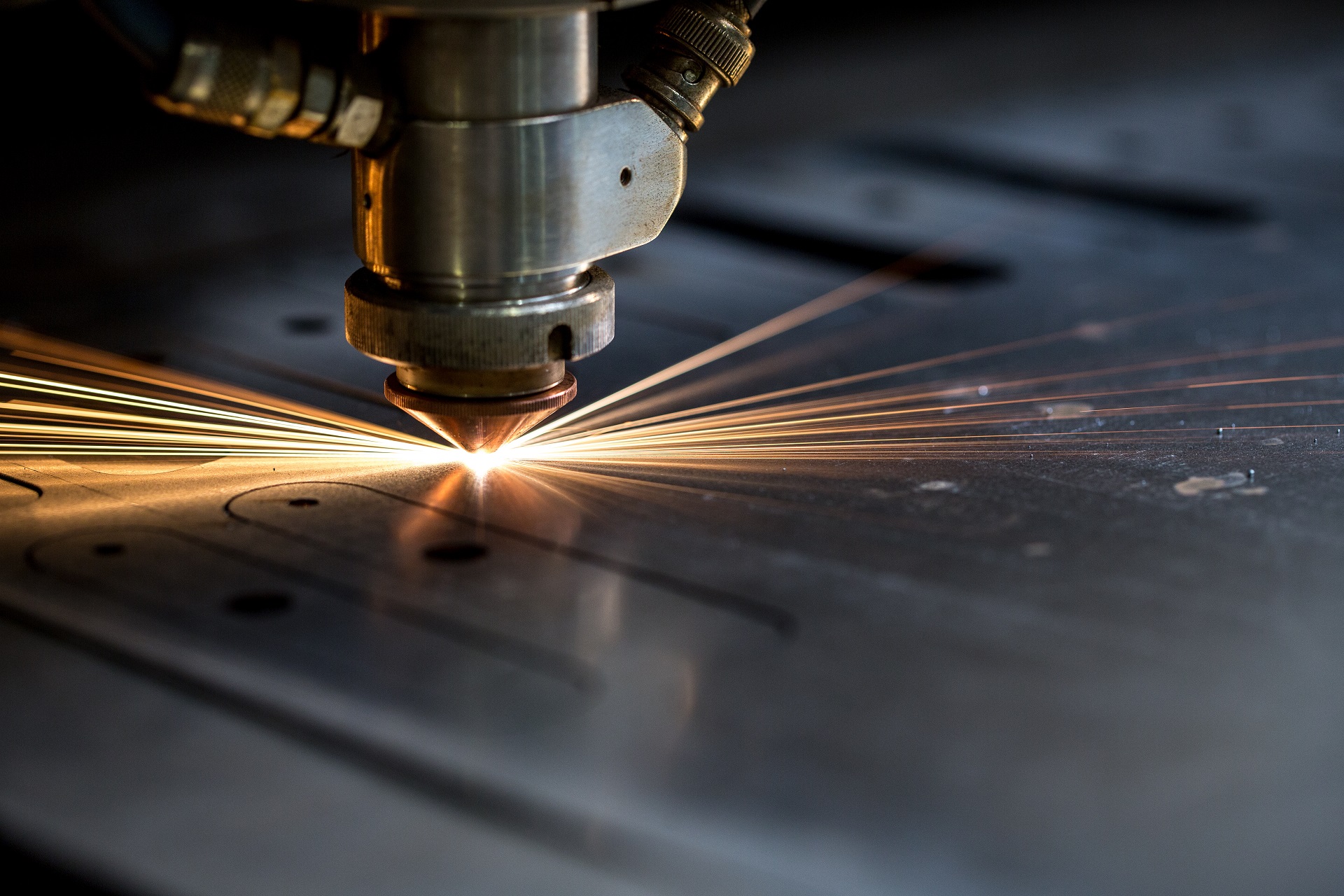
Beispielhafte Verfahren im Überblick
gratbehaftete
Fertigungsverfahren
- Bohren
- Brennschneiden
- Reißen
- Sägen
gratlose
Fertigungsverfahren
• Scherschneiden (teilweise)
• Wasserstrahlschneiden
Form, Volumen und Höhe (Ausmaß) des Grats hängen dabei grundsätzlich von der genauen (metallurgischen und geometrischen) Art des Werkstücks und des Werkzeugs ab. Darüber hinaus spielt die Art und Weise eine Rolle, wie das trennende Verfahren durchgeführt wird. Aus diesem Grund ist es teilweise möglich, unter Beibehaltung aller Faktoren lediglich durch Justieren – etwa der Arbeitsgeschwindigkeit – die Gratbildung zu reduzieren.
Zudem hat bei vielen Verfahren die Schärfe des bearbeitenden Werkzeuges einen erheblichen Anteil an der Gratbildung. Je größer die Schärfe, desto geringer das Maß der Gratbildung und dessen Ausprägung.
Die Auswirkungen von Graten in der Fertigung
Grate können die Qualität des Erzeugnisses negativ beeinflussen und deshalb weitere Bearbeitungsschritte notwendig zu machen, um eine höhere Güte zu erzielen. Sie können verschiedene nachteilige Auswirkungen haben:
- außerhalb der Toleranzwerte liegende Abmessungen
- verschlechterte Passform
- verminderte oder gar verunmöglichte Funktion
- unsaubere und dadurch unprofessionell wirkende Optik
Zudem sind Grate in der Regel äußerst scharfkantig. Gratbehaftete Werkstücke stellen deshalb ein erhebliches Risiko für schwerwiegende Schnittverletzungen dar.
Allerdings kann es mitunter gewünscht oder vernachlässigbar sein, dass es zu einer Gratbildung kommt. Dies ist beispielsweise dann der Fall, wenn der Blechschnitt nur ein Zwischenschritt zu seiner ohnehin notwendigen präziseren Bearbeitung der Schnittfläche oder des gesamten Werkstücks ist. Besonders häufig sind solche Grate zudem bei Umformprozessen zu finden.
Die drei grundlegenden Entgratungsverfahren
Das Ziel ist es, den Grat am Ort seines Bestehens zu entfernen und dabei nach Möglichkeit nur dasjenige Material abzutragen, aus dem der Grat besteht. Andernfalls besteht das Risiko, dass das Werkstück an dieser Kante untermaßig wird.
Sämtliche dafür infrage kommende Verfahren lassen sich in drei grundlegende Verfahren unterteilen:
Chemische
Entgratung
Der Grat wird durch eine künstlich herbeigeführte Elektrolyse, Verätzung oder Korrosion entfernt.
Mechanische
Entgratung
Der Grat wird durch ein spanendes oder zerteilendes Fertigungs-verfahren entfernt.
Thermische
Entgratung
Der Grat wird bis über seinen Schmelzpunkt erhitzt und dadurch entfernt.
Welches Verfahren zum Einsatz kommt, hängt dabei sowohl von der Art des Werkstücks und des Grats ab als auch von den notwendigen weiteren Bearbeitungsschritten und der dadurch definierten Wirtschaftlichkeit.
Ganz ähnlich wie bei anderen Fertigungsverfahren wird das Entgraten ebenfalls in gezielt und ungezielt wirkende Verfahren unterteilt. Die letztendlichen Einteilungen sind zudem hier die Fertigungsverfahren nach DIN, sprich:
- Zerteilen
- Spanen mit geometrisch bestimmter Schneide
- Spanen mit geometrisch unbestimmter Schneide
- Abtragen
Wichtige chemische Entgratungsverfahren im Überblick
Elektropolieren
Das Elektropolieren gehört zu den elektrochemischen Prozessen. Hierfür ist eine Stromquelle notwendig. Grundsätzlich funktioniert dieses Verfahren nur bei elektrisch leitfähigen Materialien und ist eher für die Feinentgratung zweckmäßig. Es lässt sich gegebenenfalls als zweiten Entgratungsschritt einsetzen, wenn dies aus wirtschaftlichen Gründen notwendig ist oder sinnvoll erscheint.
Beim Verfahren wird das Werkstück in eine elektrochemische Zelle integriert. Stark vereinfacht gesprochen wird das metallische Werkstück (oft nur der Grat bis zur gewünschten Schnittkante) in eine elektrolytische Flüssigkeit eingetaucht; typischerweise eine wässrige Säure-Wasser-Lösung.
Dann wird das Werkstück mit dem Minus-Pol einer Gleichstrom-Spannungsquelle verbunden. In möglichst großer Entfernung dazu findet sich ein metallisches Gegenstück, das an den Plus-Pol angeschossen ist. Fließt Strom, wandern Elektronen allmählich vom Werkstück zum „Opfer-Werkstück“. Dadurch wird der Grat nach und nach abgetragen.
Aufgrund der aggressiven Natur der Elektrolytlösung wird dieses Verfahren vornehmlich bei nichtrostenden Metallen angewandt.
Chemisches Entgraten
Während das Elektropolieren ein elektrochemisches Verfahren darstellt, werden alle anderen Verfahren, bei denen kein elektrischer Strom fließt, als herkömmliche chemische Entgratungsverfahren bezeichnet.
Dabei kommt eine abgestimmte ätzende oder korrodierende Flüssigkeit als Tauchbad für das Werkstück zum Einsatz. Zusammensetzung und Einwirkzeit unterscheiden sich durch
- die metallurgische Zusammensetzung,
- das Ausmaß der Gratbildung,
- das Maß der gewünschten Entgratung und
- die Empfindlichkeit des gesamten Werkstücks.
Der Grat wird dabei weggeätzt oder -korrodiert. Dies ist insbesondere für solche Werkstücke bedeutend, die eine komplexe Oberflächengeometrie aufweisen, durch die es nicht (wirtschaftlich) möglich ist, den Grat mit anderen Verfahren zu beeinflussen.
Bürsten
Bei diesem Verfahren kommen (Draht-)Bürsten zum Einsatz. Ihre Formgebung definiert sich durch die Geometrie des Werkstücks. Die Borsten bestehen aus einem härteren Material als der Grat und tragen ihn durch gerad- oder krummlinige Bewegung ab.
Dabei muss entweder durch das gewählte Einspannverfahren oder eine Bewegungsbegrenzung sichergestellt werden, dass nur der Grat bearbeitet werden kann. Ähnlich wie bei allen anderen mechanischen Entgratungsverfahren besteht andernfalls das Risiko, dass die Schnittkante selbst in unerwünschtem Ausmaß abgetragen wird.
Fräsen
Fräsen ist heute eines der gängigsten Verfahren zum mechanischen Entgraten von Metallteilen. Zwei- oder dreidimensional steuerbare CNS-Fräsen werden dazu mit einem Fasenfräser bestückt. Er sorgt für eine Spanabhebung entlang der Schnittkante, welcher der Grat zum Opfer fällt.
Das Verfahren lässt sich einfach in einen automatisierten Fertigungsprozess integrieren und die anfallenden Späne können für ein Recycling leicht gesammelt werden.
Gleitschleifen
Grate haben die Eigenschaft, deutlich dünner und weicher zu sein als das Material des Werkstücks. Insbesondere bei kleinen bis mittleren Werkstückgrößen und in der Serienfertigung wird deshalb das Gleitschleifen herangezogen (nach DIN als Gleitspanen bezeichnet).
Bei diesem Verfahren, das unter Fachleuten auch als Trowalisieren bekannt ist, wird ein oder mehrere Werkstücke in einen Behälter gegeben. Dieser kann durch einen Antrieb oszillieren, vibrierend oder ist auf ei ne andere Weise in der Lage, sich zu bewegen.
Zusammen mit den Werkstücken werden Schleifkörper mit definierten geometrischen Formen, Körnungen und Härtegraden in den Behälter eingefüllt. Typischerweise wird zudem eine Flüssigkeit eingefüllt. Sie ergibt zusammen mit den Schleifkörpern den sogenannten Compound.
Durch die Bewegung des Behälters werden die Schleifkörper immer wieder über die gesamte Werkstückoberfläche geführt. Der weiche Grat wird dabei als erstes abgetragen. Allerdings bleibt auch das restliche Material nicht unberührt, sodass einerseits eine sehr gezielte Zeitsteuerung erfolgen muss und andererseits gegebenenfalls weitere Nachbearbeitungsschritte erforderlich sind.
Wirtschaftlich wird das Verfahren zudem von der Größe des Werkstücks limitiert.
Strömungsschleifen/Druckfließläppen
Das Gleitschleifen findet nicht zuletzt eine Begrenzung in der Komplexität der Werkstückform. Ist diese zu groß, kann es mitunter zu lange dauern, bis alle Grate abgetragen sind. In dem Fall würde der (besser erreichbare) Rest der Oberfläche zu stark in Mitleidenschaft gezogen.
Beim Strömungsschleifen wird deshalb eine abrasive, pastöse Masse verwendet. Deren Viskosität ist auf Art und Dicke des Grats abgestimmt. Dazu wird das Werkstück in zwischen zwei Zylinder eingespannt. Ein beweglicher Kolben schiebt die Schleifmasse durch das Werkstück in den oberen Zylinder. Ist der Kolben an seinem oberen Totpunkt angelangt, bewegt er sich wieder nach unten und saugt die Masse an.
Durch die steuerbare Viskosität können selbst sehr komplexe Blechwerkstücke entgratet werden, bei denen es auf andere Weise nicht möglich ist, die Innenräume zu erreichen.
Herkömmliches Schleifen und Läppen
Diese beiden Methoden setzen auf ein bewegliches Schleifmedium, welches über die Schnittkante geführt wird. Der maßgebliche Unterschied zwischen beiden Verfahren:
Beim Entgraten von Metallblechen kommt die Wahl des jeweiligen Verfahrens vor allem darauf an, wie präzise die Schnittkante später sein muss. Durch das Verhalten des Schleifkorns beim Läppen sind hier deutlich geringere Abtragungsraten im Bereich von Mikrometern möglich.
Hochdruckwasserstrahlentgraten
Ganz ähnlich wie beim allgemeinen Wasserstrahlschneiden wird hierbei der Grat mittels eines stark fokussierten und unter sehr hohem Druck stehenden Wasserstrahl abgeschnitten. Der Druck kann bis zu 6.000 Bar erreichen, deshalb ist das Verfahren auch für dickere Grate beziehungsweise Werkstücke und selbst sehr harte Stähle wirtschaftlich.
Im Gegensatz zu den meisten anderen Verfahren findet hier zudem keine nennenswerte Erwärmung der Gratumgebung statt. Hochdruckwasserstrahlentgraten ist deshalb auch nach bereits erfolgten Härtungsprozessen anwendbar.
Wichtige thermische Entgratungsverfahren im Überblick
Laserentgraten
Das Laserentgraten stellt das thermische Gegenstück zum Hochdruckwasserstrahlentgraten dar. Hierbei wird dementsprechend der Grat durch einen hochenergetischen, fokussierten Laser abgetragen.
Prinzipiell kann dieses Verfahren zwar bei jeder Form von Blechzuschnitt angewendet werden. Aufgrund des aufwendigen Prozesses wird es jedoch üblicherweise nur bei Werkstücken angewendet, die zu empfindlich für andere Entgratungsmethoden sind.
Explosionsentgraten
Dieses Verfahren ist eher seltener, dafür aber umso spektakulärer. Es macht sich die Eigenschaft von Graten zunutze, eine (im Vergleich mit dem restlichen Werkstück) deutlich größere Oberfläche bei gleichzeitig stark verringertem Volumen aufzuweisen.
Dies wird in einer Entgratkammer genutzt – eine Art kontrollierte Sprengkammer. Das Werkstück wird von sämtlichen Verunreinigungen befreit und die Kammer danach hermetisch verschlossen. Anschließend wird ein abgestimmtes Gemisch aus Luft/Sauerstoff und einem brennbaren Gas eingeleitet – typischerweise Wasserstoff oder Alkane wie beispielsweise Methan.
Das Sauerstoff-Gas-Gemisch zündet durch einen elektrischen Impuls und es erfolgt eine Explosion. Hierbei entstehen Temperaturen von bis zu 3.000°C und mehr. Die äußerst kurze Einwirkzeit dieser Hitze im Bereich von Sekundenbruchteilen heizt den Grat wegen seiner großen Oberfläche und dem geringen Volumen ungleich stärker auf als das restliche Werkstück. So wird der Grat aufgeschmolzen und teilweise durch die Wucht der Explosion von der Schnittkante weggerissen.
Je nach notwendigem Feinheitsgrad ist es vor allem bei Eisenwerkstoffen allerdings noch notwendig, einen zweiten Entgratungsschritt mit einer anderen Methode anzuschließen, um etwaige Schlackerückstände zu entfernen.
Bildquellen
Bild 1: stock.adobe.com, © quka
Bild 2: stock.adobe.com, © Wisky
Bild 3: stock.adobe.com, © Pavel Losevsky
Bild 4: stock.adobe.com, © roostler
Bild 5: stock.adobe.com, © Pixel_B